CO2-Reduktion bei Montanuni Leoben : Zukunftswerkstoffe - Material mit Potenzial
Inhalt
- Forschung an Oxidationsschutzschichten für leichtere Turbolader
- Neue Schweißzusatzwerkstoffe für ultrahochfeste Stähle
- Linzer Forscher nutzen dielektrische Elastomere
- Die Jagd nach dem ultimativen Super-Composite aus CFK
- Neuer Turbinenstahl für langlebige Kraftwerke
- Höhere Bearbeitungsgeschwindigkeiten für Titan-Zerspanung
- Nanostrukturierte Oberflächen
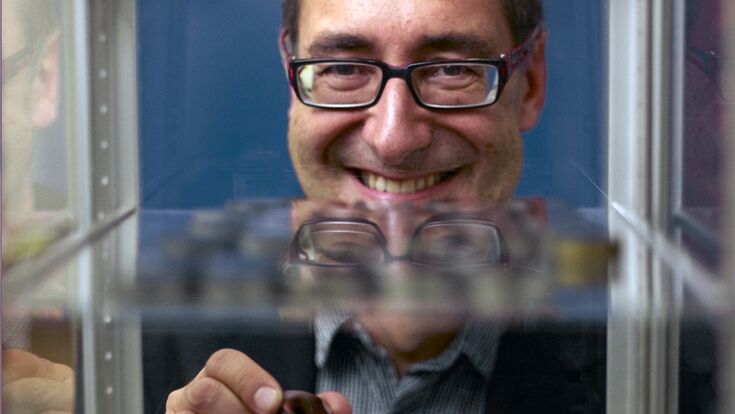
So fühlten sich Automobilbauer zuletzt. Denn ab 2012 gibt es keine Ausreden mehr: Dann setzt es Strafzahlungen für jedes Gramm Kohlendioxid, das die zulässigen C02-Werte übersteigt. Noch können sich Autobauer mit einer „Einschleifphase“ trösten – „sie knabbern aber ganz schön an der Regelung“, weiß Christian Mitterer. Er ist Oberflächenspezialist am Department Metallkunde und Werkstoffprüfung der Montanuni Leoben – und sieht drakonische Strafen auf die Hersteller zurollen: „Das wird teuer, wenn nichts passiert“, zeichnet der Werkstoffprofi ein bedrohliches Bild.Bisher waren Autobauer von allzu harschen EU-Reglementierungen befreit. Jetzt sind sie alarmiert – das zeigen die Anfragen beim Ranshofener Aluhalbzeugehersteller Amag: Stahl soll weiter aus dem Auto gedrängt werden. Anfragen häufen sich aber auch an Mitterers Department.
Nie mehr die wichtigsten News aus Österreichs Industrie verpassen? Abonnieren Sie unser Daily Briefing: Was in der Industrie wichtig wird. Täglich um 7 Uhr in Ihrer Inbox. Hier geht’s zur Anmeldung!
Forschung an Oxidationsschutzschichten für leichtere Turbolader
Der feinsinnige Wissenschaftler erforscht Oxidationsschutzschichten für Titanaluminide. Aus letzterem intermetallischem Material könnten noch leichtere Turbolader entstehen, die schneller die Enddrehzahl (bis 300.000 Umdrehungen pro Minute) erreichen. Sie sollen einem effizienteren Verbrennungsprozess den Weg ebnen. Damit kein Sauerstoff an ihre Oberfläche gelangt, gibt es Schutzschichten – etwa aus Aluminiumoxiden. Mitterers Aufgabe ist es, sie stabil und dicht zu halten. „Ein aufregendes Gebiet“, sagt der Forscher, der nun auch Rissursachen an den Schichten untersuchen will. Seit November erforscht Mitterer den Werkstoff in noch engerer Kooperation in einem Prestigeprojekt („Research Studio“). Mit an Bord: Der Laakirchener Autozulieferer Miba. Auch die Gmundener hofffen auf den baldigen Durchbruch. Mitterers gute Nachricht: „In den nächsten drei Jahren soll es soweit sein“. Ideenbörse.
Lesen Sie dazu auch: Stahl: Produktion in Deutschland fällt auf niedrigsten Wert seit 1989
Materialfortschritte auf dem Fließband: Das wünschen sich viele in der Industrie, wie das Gezerre deutscher Autobauer um den Graphitehersteller SGL Carbon zeigt. Auch bei heimischen Werkstoffwissenschaftlern fand eine Kursänderung statt. „Früher fassten wir Projekte mit der Industrie als gefährliche Drohung auf“, sagt Christian Mitterer von der Montanuni Leoben. Heute geht das wegen der stotternden Finanzierung der Hochschulen nicht mehr so leicht. „Die Arbeitsplätze unserer 35 Mitarbeiter sind großteils drittmittelfinanziert“, so Mitterer. Immer mehr Materialforscher würden „Industrieprojekte abarbeiten“. Doch auf welche Zukunftswerkstoffe schielt die heimische Industrie? INDUSTRIEMAGAZIN sah sich am Werkstoffsektor um – und war überrascht: Viele der jetzt erforschten Materialien stehen kurz vorm Sprung in die erste Werkstoffliga.
Neue Schweißzusatzwerkstoffe für ultrahochfeste Stähle
Fügetechnik: Zusatzstoffe für Schweiß-Normalos. Stahlerzeuger wollen das Handling ultrahochfester Stähle mit neuen Schweißzusatzwerkstoffen revolutionieren. Ein Candlelight-Dinner mit dem Vorstand? Muss man sich erst einmal verdienen. Im Falle der voestalpine-Entwickler ist dafür ein schöner Durchbruch auf dem Werkstoffsektor hilfreich. Der nicht alle Tage gelingt. Aber der sich in Linz schon leise ankündigt: „Wir haben Glück – es ist bald wieder soweit“, erzählt Forschungschef Peter Schwab und lächelt wissend. Nach Jahren des vorsichtigen Vortastens sind die Linzer in der Entwicklung (ultra)hochfester Stähle angekommen. Die Stähle – sie frappieren mit einer Streckgrenze von 700 Megapascal aufwärts – machen besonders Kranbauer unruhig wie ein kleines Kind: Kranschubarme könnten belastbar wie noch nie gebaut werden. „Wir überwanden dazu das Henne-Ei-Problem“, erklärt Schwab. Denn lange redeten sich Stahlhersteller reflexartig auf die mangelnde Unterstützung der Hersteller von Schweißzusatzwerkstoffen – in dem Fall sogar die Konzerntochter Böhler Welding – aus: Wenn es keine Möglichkeit gibt, hochfeste Stähle zu verbinden, brauche man sie „gar nicht erst entwickeln“, kennt Schwab die Argumentationslinie. Umgekehrt fragten sich die Lieferanten von Schweißzusätzen zu Recht: Wozu etwas entwickeln, wenn es noch nicht einmal die Anwendung – den Stahl – dafür gibt? „Das war verzwickt“, so Schwab.
Lesen Sie dazu auch: Fronius – als Photovoltaik die Schweißtechnik überholte
Die Problematik durchbrachen die Linzer in einem gemeinsamen Projekt mit Böhler Welding. Zusatzwerkstoffe sind fürs (Schutzgas-)Schweißen gedacht – genau solche entwickelt man zusammen. Sie enthalten eine Menge Eisen und Legierungselemente wie Chrom-Molybdän. Ihre Funktion: „Sie stellen die Spaltüberbrückung sicher“, weiß Schwab. Bei hochfesten Stählen sei die Auslegung der Schweißparameter allerdings „schwieriger“, erklärt Rudolf Rauch, voest-Fachbereichsleiter Schweißen Warmband – deshalb die „Maßschneiderung“ der Zusätze. Für Stähle bis 900 Megapascal Streckgrenze gibt es sie bereits. Nun wollen die Linzer, die schon unzählige Risstests durchführten, „die 1100er-Grenze knacken“, bestätigt Schwab. Die Industrie – etwa Kranhersteller wie Palfinger oder Liebherr – interessiert das brennend: Neue Zusätze könnten auch bei 1100er-Blechen den schweißbaren Bereich und die Abschmelzleistung um ein Drittel vergrößern. Erfreuliche Konsequenz: Auch schlechtere Schweißer würden so „sehr gute Ergebnisse“ erzielen, meint Schwab.
Linzer Forscher nutzen dielektrische Elastomere
Robotik: Empfindsame Teile-Taster.Mit dielektrischen (nichtleitenden) Elastomeren wollen Linzer Forscher Maschinen das Fühlen beibringen – Roboterbauer sind betört. Für einen Knalleffekt sorgte eine Publikation im Jahr 2000 am kalifornischen SRI International Institut: Sie zeigte, dass sich Elastomere – verformbare Kunststoffe – bis aufs Doppelte ihrer Fläche ausdehnen können. „Und zwar durch Anlegen einer elektrischen Spannung“, erzählt Siegfried Bauer, Forscher in der Abteilung Physik weicher Materie der Uni Linz. Auch für Bauer ein Wow-Effekt – deshalb nahm er 2005 eine Gastprofessur in Finnland an. Dort entwickelte er einen dreidimensionalen Aktuator aus Gummi, der sich durch Anlegen einer Spannung „wie eine Hand öffnen und schließen ließ“, so Bauer. Zurück in Österreich, blieb er seinem – mittlerweile sehr lieb gewordenem – Thema treu: Der Forscher untersucht weiter, wie sich mit elektrischen Feldern Verformungen an Elastomeren erzeugen lassen.
Lesen Sie dazu auch: Fügeverfahren in der Industrie: Ein Blick auf optimale Klebelösungen
Die Grundidee ist simpel: An einem Elastomer – etwa einer 3M-Klebefolie mit dreifacher Stärke eines Blatt Papiers – werden an beiden Seiten Elektroden aufgebracht. Bei Aufladung der Elektroden zieht die positiv geladene Oberseite die negativ geladene Unterseite an – „und den Gummi drückt es zusammen“, erklärt Bauer. Dabei bleibt das Volumen gleich, das Elastomer dehnt sich in der Fläche aus. Klingt einfach – hat jedoch das Zeug zu einer kleinen Revolution in der Robotik: Feinfühlige Roboter sind in der Industrie schon länger ein heißes Eisen.
Lesen Sie hier noch: Robotik in der Industrie: Vom Unimate zum LLM
So hat der Linzer Roboterhersteller FerRobotics schon vor einiger Zeit Roboter mit Muskeln umgesetzt – allerdings auf Basis von Druckluft. Auch die elektrische Deformation findet Geschäftsführer Ronald Naderer hochspannend: „Wir testen sie sicher, sobald sie die Forschungslabore verlassen hat“, spendet er schon jetzt Applaus. Fühlende Roboter wären nach Bauers Meinung vielleicht ganz gut in Labors oder Industrie-Reinräumen aufgehoben: Dort, wo der Roboter wegen fragiler Teile nicht so einfach „zupacken kann“, glaubt er.Zwei Herausforderungen halten den Forscher derzeit auf Trab: Der Aktuator – also der Greifer – könnte gleichzeitig als Sensor in Aktion treten. So könnte man die „Kräfteinformationen nutzen“, hofft Bauer. Und es ist noch unklar, welche Materialien überhaupt in der Pole Position stehen sollen. „Natürliche Elastomere wären toll“, so Bauer. Aus dem Grund arbeiten die Linzer eng mit der Harvard-Universität zusammen. „Wir testen, die Amerikaner machen die Modellberechnungen“, erklärt Bauer. Zuletzt gelang dem Forscher ein viel beachteter Nachweis: Man dehnte Elastomere in ihrer Fläche „um 1700 Prozent aus“.
Die Jagd nach dem ultimativen Super-Composite aus CFK
CFK Flugzeug-Leichtbau: Suche nach dem Super-Composite.Faserverstärkte Kunststoffe starteten in der Luftfahrtindustrie durch – jetzt steigt der Kostendruck: Die Suche nach maßgeschneiderten Komponenten läuft an. Werkstoffe, die einen mürbe machen: Solange man „in der Substanz weiterkommt“, hat Heinz Pettermann, Forscher am Institut für Leichtbau und Struktur-Biomechanik der TU Wien, mit ihnen kein Problem. Der Wissenschaftler trägt derzeit alles andere als Schwermut im Herzen – auch wenn seine Arbeit vom Plot her kein Leichtgewicht ist: Pettermann beschäftigt sich mit kohlenstofffaserverstärkten Kunststoffen, kurz CFK. Dieser Werkstoff mauserte sich zuletzt zum Überflieger im Luftfahrtbereich: Flugzeughersteller wie Boeing oder Airbus gehen mehr und mehr dazu über, ihn im Flieger – sogar bei tragenden Strukturen – einzusetzen.
Nun will Pettermann in einem aktuellen Projekt das Wissen um CFK-Werkstoffe um einige Facetten anreichern. „Es geht um maßgeschneiderte Werkstoffe“, erzählt der Forscher. Denn auch wenn der Einsatz von Karbon in der Luftfahrt als epochaler Wurf durchgeht: Ein Quantensprung wäre eigentlich erst „die ideale Verteilung von Kohlefasern im Bauteil“, weiß Pettermann. Die Begründung: Die derzeit verbauten Composites hätten in Längsrichtung gute Eigenschaften – „in ein paar Querrichtungen aber vielleicht zu gute“, blickt Pettermann durch die kaufmännische Brille seiner Auftraggeber. Und verrät, was seine Arbeitsgruppe tut: Sie stellt ein Berechnungsmodell auf die Beine, das aus der Reihe tanzt: Bisherige Berechnungsmethoden zur Vorhersage elastischer Bauteileigenschaften seien „rechenintensiv“, erklärt der Forscher. Er selber wolle deshalb die innere Struktur von CFK-Geweben „durch Schalenelemente modellieren“.
Lesen Sie hier noch: Quantentechnologie in der Industrie: ihr enormes Potenzial
In einem Durchgang könnte so „das komplette richtungsabhängige Versagensverhalten eines Teils simuliert werden“, hofft der Forscher. Mit Hinblick auf das CFK-Flechten – ein neues Herstellungsverfahren, bei dem schon ein Halbzeug in der endgültigen Bauteilform entsteht, – wäre das speziell für den Rieder Luftfahrtzulieferer FACC interessant. „Die Geflechtsgeometrien sind hier noch komplexer – und gehören natürlich überprüft“, so Pettermann. Ein richtiger Flugzeugnarr ist der Forscher eigentlich nicht. Er will lieber die Prozesse im Werkstoff verstehen – das sei seine „Motivation“, sagt er. In ein paar Jahren schon könnte sein verfeinertes Modell in der Praxis ankommen – „etwa im Prototypenbau“, schätzt Pettermann. Die Luftfahrtindustrie ist schon in Lauerstellung: Zulieferer wie FACC hätten endlich ein Instrumentarium zum schnelleren Designen von CFK-Bauteilen in der Hand. Angesichts anziehender Auftragslage eine feine Sache: „Pettermanns Arbeit ist für uns ein echter Mehrwert“, so F&E-Leiter Martin Fleischmann.
Neuer Turbinenstahl für langlebige Kraftwerke
Kraftwerksbau: Turbinenstahl mit Langzeit-Charme. Ein neuer Werkstoffmix könnte die Lebensdauer von Kraftwerken erhöhen – Wiener Forscher liefern die Instrumente. „Dafür nehme ich mir bis zur Pensionierung Zeit“. Ernst Kozeschnik – ehmals TU Graz – denkt in großen Zeiträumen. Der Leiter des Instituts für Werkstoffwissenschaft und Werkstofftechnologie an der TU Wien entwickelte ein Simulationswerkzeug, das in der Industrie viel Lob erfährt: Sein Tool erlaubt Vorhersagen über die Ausscheidungsentwicklung in Werkstoffen. Ein Hilfsmittel, das Kraftwerke von Siemens oder Alstom effizienter macht – denn nur die richtige Werkstoffwahl sorgt bei Dampfturbinen für eine optimale Lebensdauer von mehr als 100.000 Betriebsstunden.
Je höher der Druck (mehr als 300 bar) und die Dampftemperatur (620 Grad), umso größer der Wirkungsgrad der Turbine. Für das Turbinengehäuse und die zugehörigen Rohrleitungen braucht es also eine ziemlich robuste Schale: „Neun- bis zwölfprozentiger Chromstahl eignet sich besonders gut“, weiß Kozeschnik. Martensit indes bildet im Werkstoff eine feine kristalline Substruktur, die dem Stahl seine hohe Grundfestigkeit gibt“, erklärt der Forscher. Ausscheidungen stabilisieren diese Mikrostruktur – leider aber gibt es nicht nur „gute“ ihrer Art. Ein richtiger Übeltäter ist die Z-Phase, „eine Kristallstruktur mit Vanadium, Chrom und Stickstoff“, erklärt Kozeschnik. Ihr gilt sein größtes Augenmerk: Sie kann Kraftwerksrohre nach Jahren plötzlich platzen lassen, indem sie „gute“ Ausscheidungen wie Vanadiumnitride „einfach auffrisst“. So selten die Phase auftritt: In der Industrie – namentlich auch beim Turbinenfertiger voestalpine Gießerei – ist sie extrem gefürchtet.
Deshalb verfeinert Kozeschnik jetzt sein Werkzeug. Bisher arbeitete sein Simulationswerkzeug mit Mittelwerten. Jetzt sollen auch lokale Effekte – etwa die inhomogene Verteilung nach dem Gießereiprozess – „mitberücksichtigt werden“, so die strammen Ziele des Wiener Forschers. Ein verbessertes Simulationstool könnte die Karten auf dem Werkstoffsektor neu mischen: Derzeit läuft fieberhaft die Suche nach alternativen Legierungskonzepten. Auch der Trick, aus „bösen“ Ausscheidungen „gute“ zu machen, könnte funktionieren“, so Kozeschnik. Die Industrie sieht Kozeschniks ständig weiterentwickeltes Tool als Bereicherung an: „Ein sensationelles Werkzeug“, sagt Reinhold Hanus, F&E-Leiter bei voestalpine Gießerei.
Höhere Bearbeitungsgeschwindigkeiten für Titan-Zerspanung
Eisenbasis-Legierungen (Wälz-)Fräsen: Wunsch-Schneidstoffe für die Schwerzerspanung. Ein neuer kohlenstofffreier Schneidstoff verspricht um ein Drittel schnellere Bearbeitungsgeschwindigkeiten beim Zerspanen von Titan – „good news“ für Lohnfertiger. „Wir haben einen neuen Schneidstoff in der Pipeline“: Ingo Siller ist Forschungsleiter bei Böhler Edelstahl – und er hat eine gute Nachricht für Betriebe, die schwer zerspanbare Materialien wie Titan bearbeiten. Mit einer Neuentwicklung will der Betrieb spektakulär die Lücke zwischen Schnellarbeitsstahl und Hartmetall schließen. Denn beim Fräsen von Titan- sowie Nickelbasis- oder austenitischen Legierungen ist man mit Schnellarbeitsstahl auf Geschwindigkeiten von rund 200 Meter pro Minute begrenzt.
Lesen Sie hier noch: Thyssenkrupp – Weniger CO2 bei Stahlproduktion
Mit dem neuen Schneidstoff sollen um ein Drittel höhere Geschwindigkeiten möglich sein – „ohne dass der Fräser massiv verschleißt“, so Siller. Unzählige Testläufe mit Legierungen fanden dafür schon bei den Kapfenbergern statt – metallographische Untersuchungen und labortechnische Tests. Der neue Schneidstoff soll das Bearbeitungstempo um ein Drittel erhöhen. Böhler-Mann Gert Kellezi: Die Industrie darf mit einer „speziellen Legierung ohne Kohlenstoff“ rechnen. Eisen, Molybdän und Kobalt sind Mitbestandteile – für die hohe Festigkeit sorgen nanometerfeine Ausscheidungen von intermetallischen Phasen. 2012 wird es den Schneidstoff geben. Ein oberösterreichischer Lohnfertiger zeigte sich auf INDUSTRIEMAGAZIN-Anfrage sofort interessiert: „Darauf warten wir“.
Nanostrukturierte Oberflächen
Mikroelektronik: Halbleiter, die stempeln gehen. Forscher loten die Grenzen der Nanostrukturierung von Oberflächen per Stempeltechnologie aus – Nutznießer könnte die Chipindustrie sein. Die Elektronenstrahl-Lithographie zur Herstellung kleinster Oberflächenstrukturen hat viele Stärken – und einen wunden Punkt: Das Strukturieren eines Chips mit 20 Nanometer großen Elementen – etwa Kondensatoren – „ist ziemlich zeitaufwendig“, erzählt Michael Mühlberger vom Forschungsinstitut Profactor. Der Wissenschaftler verfolgt einen alternativen Ansatz – die so genannte Nanostrukturierung per Stempel (Nanoimprint Lithography, NIL). Neben der Biophyisk und Optik findet sie auch in der Chipindustrie immer stärker Gehör. Das Verfahren ist hochspannend – es gibt aber noch Forschungsbedarf: Ein UV-aushärtendes Material, etwa das Silikon POSS (polyhedrales oligomeres Silsesquioxan), wird mittels Stempel auf einem Substrat (Wafer) für elektronische Bauteile strukturiert. Anschließend wird der Stempelvorgang einfach beliebig oft wiederholt. „Das geht blitzschnell“, so Mühlberger, der die derzeitigen Problemzonen mittlerweile ganz gut kennt: „Das aufzubringende Material sollte nicht am Stempel kleben bleiben“, gibt er ein Beispiel.
Lesen Sie dazu auch: EU-Chips Act: Wie können Investitionen nach Österreich geholt werden?
Deshalb spielt sein Team unterschiedlichste Möglichkeiten durch – und zieht Interesse auf sich: Der steirische Chiphersteller austriamicrosystems behält die forscherischen Bemühungen „genau im Auge“, bestätigt Franz Schrank, R&D-Projektleiter in Unterpremstätten. Denn auch wenn das Thema noch ein „Stück weit weg“ sei: Das Stempeln könnte in Zukunft ganz gute Karten in der Chipproduktion haben. Im Bereich von 20 Nanometern wird die Lithographie nur noch „unter Aufbringung enormer Mittel möglich“, weiß Mühlberger. Intel zeigte dies unlängst mit einer Millioneninvestition in Anlagentechnik. Das neue Verfahren könnte Nanostrukturen weitaus günstiger auf den Chip bringen. Doch darum geht es Franz Schrank von austriamicrosystems weniger. Was ihm eher zusagt: In ein- und demselben Prozess könnten – einen mehrlagigen Stempel vorausgesetzt – „3D-Strukturen hergestellt werden“, so Schrank. Bei Profactor bleibt man auf Linie: Zuletzt gelang mit Partnern in einem Projekt („NILaustria“) die Strukturierung von zwölfeinhalb Nanometer kleinen Strukturen – fast acht Millionen in einem Stempelschritt. Mühlberger: „Da klopfte uns das Herz“.