Fertigung : Tough guys: Das sind die besten Fabriken Österreichs
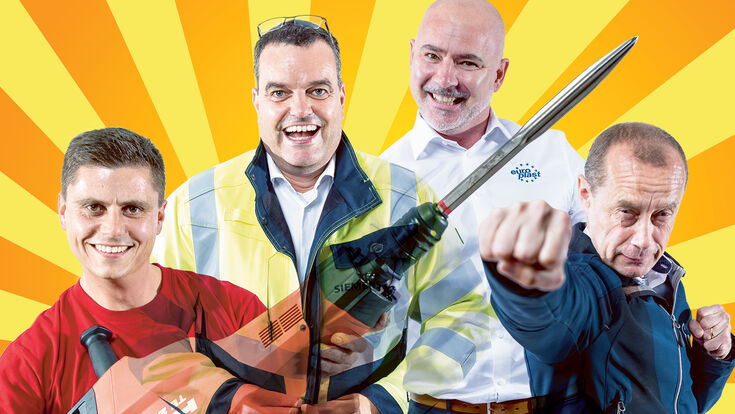
So sehen Sieger und Beinahesieger aus: Christoph Holzer, Leiter Operations des Siegerwerks Hilti AG Zweigniederlassung Thüringen; Sven-Oliver Fischer, kaufmännischer Leiter Siemens Mobility, Werk Simmering; Arthur Primus, CEO Europlast und Christian Kapper, Montageleiter Koenig & Bauer (AT)
- © Matthias HeschlAktive Mitgliedschaft erforderlich
Das WEKA PRIME Digital-Jahresabo gewährt Ihnen exklusive Vorteile. Jetzt WEKA PRIME Mitglied werden!
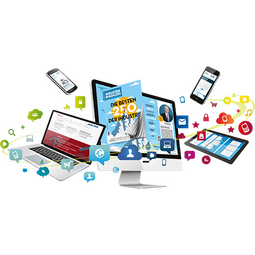
Sie haben bereits eine PRIME Mitgliedschaft?
Bitte melden Sie sich hier an.
Sie kamen von weit her: dem Westen Österreichs, der Bludenzer 2.300-Einwohner-Gemeinde Thüringen, Werkstraße 13. Selbst eine (harmlose) Autopanne konnte sie nicht stoppen. Ziel: Das nordwestliche Waldviertel, genauer: die grenznah zu Tschechien liegende Stadt Gmünd. Ein Naturjuwel, aber auch Austragungsort des Finales von Fabrik2022.
Ebendort wollten es Christoph Holzer, Leiter Operations und Paul Scholz, Head of Digital Transformation dann noch einmal wissen: Wo liegt Hilti Thüringen im branchenübergreifenden Vergleich? Die Standortbestimmung war - das wissen wir heute - eine erfreuliche. Die Produktionsmanager sind um eine Trophäe reicher, jener zur Auszeichnung der "Fabrik des Jahres". Das kommt nicht von ungefähr.
600 Mitarbeiter, 80 Lehrlinge. 38 unterschiedlichen Montagelinien für die Komponenten- sowie Endmontage von Werkzeugen für Bohr- und Abbrucharbeiten, das Sägen und Direktbefestigen. Hilti Thüringen zählt zu den größten und wichtigsten Produktionsstandorten des Hilti-Konzerns.
1970 wurde das Werk gegründet, 2009 zuletzt nochmals erweitert. Über 80 Prozent der Hilti-Mitarbeiter in Thüringen empfehlen anderen das Unternehmen als großartigen Arbeitgeber. Mit engagierten Teams sowie einer Werkzeug-Prototyp-Fertigungsanlage trägt das Werk wesentlich zur Einführung neuer, innovativer Produkte bei. 2009 wurde der Standort zum besten Ausbildungsbetrieb Österreichs gekürt. Auch sonst performt er auf allen Ebenen. "Ein grandioses Werk - und ein ebenso grandioses Team", verlautete aus Jurykreisen.
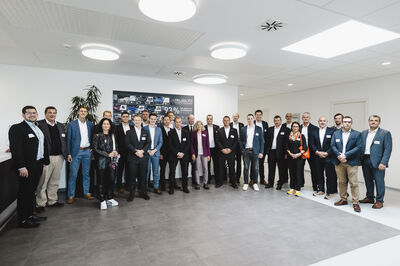
Der Wettbewerb Fabrik2022 in Zahlen
Das macht Fabrik2022 zum härtesten Produktionwettbewerb Europas
8 Unternehmen traten an.
400 Kennzahlen wurden im Rahmen der Selbstevaluierung abgefragt.
80 Fragebogen-Seiten prüfte Fraunhofer Austria insgesamt.
5 Unternehmen evaluierte Fraunhofer Austria in den Produktionen vor Ort.
220 Stunden evaluierte Fraunhofer Austria insgesamt (inklusive Vor- und Nachbereitung).
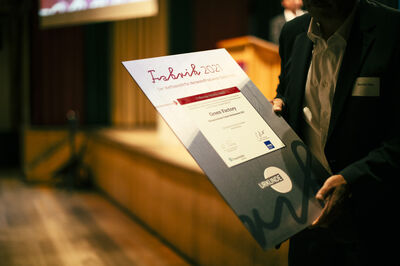
Entdecken Sie jetzt
- Lesen
- Videos
-
Podcasts
- Fiat, Lancia, Alfa Romeo, Maserati: Die Problemkinder von Stellantis in Italien | INDUSTRIEMAGAZIN 20.08.2025
- Megafusion geplatzt: Wie China an der Konsolidierung der Autoindustrie scheitert | INDUSTRIEMAGAZIN 13.08.2025
- Bosch, Continental, ZF Friedrichshafen: Deutsche Autozulieferer im Krisenmodus | INDUSTRIEMAGAZIN 06.08.2025
Härtetest. Mit Chance zur Auszeichnung.
Herausragende Leistungen in der Produktion und Logistik, Wandlungsfähigkeit, Wille zur Optimierung: Fünf Unternehmen aus ganz Österreich zogen heuer ins Finale von Fabrik2022, Europas härtestem Produktionswettbewerb, ein. Mit produktionssportlichen Spitzenleistungen, die es sonst kaum wo zu sehen gibt. Der Wettbewerb schreibt auch in seinem zwölften Jahr die spannendsten Geschichten, wie schon die Vor-Ort-Evaluierungen gezeigt haben. Auch deshalb, weil Produktionen jetzt, in den heftigen Umbruchphasen unserer Zeit, nicht die Ruhe des Seins, sondern die Spannung eines veränderlichen Zustands charakterisieren.
Lesen Sie auch: Bernhard Schinkowitsch, Principal Advisor Digital Production, Atos Österreich, im Interview
Und so wurde der von INDUSTRIEMAGAZIN und Fraunhofer Austria verliehene Produktionsaward zum Schaulaufen von ziemlich herausragenden Produzenten: Die Produktionsmanager von Europlast Kunststoffbehälterindustrie, Hilti AG, Zweigniederlassung Thüringen, Koenig & Bauer (AT), NBG Fiber sowie Siemens Mobility Austria brachten die Jurymitglieder zum Staunen. Sei es durch eine tief in der DNA verflochtene Lean-Kultur, einmalige Elemente der digitalen Prozessteuerung, oder perfekt austarierte Warenströme.
GESAMTSIEG + KATEGORIESIEG EFFICIENT FACTORY: Hilti AG, Thüringen - Die virtuosen Variantenfertiger
Auf einen durchschnittlichen Mitarbeiter im Hilti-Werk Thüringen fallen 1,5 KVP-Vorschläge pro Jahr. Auch sonst machen die Vorarlberger vieles richtig.
In der Werkstrasse 13 in der Bludenzer Gemeinde Thüringen ist Hiltis größter Standort für Montage, Zerspanung und Wärmebehandlung für die Produktion von Bohr- und Meisselhämmern, Direktbefestigungs- und Diamantgeräten als auch halbautonomen Bohrrobotern domiziliert. Jährlich rund 500.000 Geräte aus 55 unterschiedlichen Produktfamilien werden hier gefertigt. Alle erdenklichen Zerspanungsprozesse - auf über 100 Maschinen - beherrschen die Vorarlberger.
Lesen Sie auch hier zum Sieg von Hilti im Wettbewerb!
Auf einer Fläche von 42.000 Quadratmetern sind 38 unterschiedliche Montagelinien installiert, sie werden "dort mehrfach belegt, wo ähnliche Gerätetypen entstehen würden", erzählt Christoph Holzer, der hiesige Leiter Operations bei Hilti in Thüringen. Operative Exzellenz, das weiß er nur zu gut, könne allein durch Kombination optimal abgestimmter Lean- und Digitalisierungsprozesse erreicht werden.
Und da trifft es sich gut, das Thüringen auch Leitwerk für Digitalisierung ist: Sämtliche Montagelinien sind an ein MES-System angebunden, der Rollout dieser Software gelang in Rekordzeit, "unter einem Jahr", erzählt Paul Scholz, Head of Digital Transformation im Hilti-Werk in Thüringen. Visuelle Assistenzsysteme und Dashboards unterstützen Werker an ihren Arbeitsplätzen und sogar Machine Learning wird in ersten Anwendungen genutzt. Werkstück-, Werkzeug- und Maschinendaten "analysieren wir für die Prozess- und Produktoptimierung", sagt er.
Nachhaltigkeit durchdringt Unternehmen
Energetisch ist die erste außerhalb der Landesgrenzen von Liechtenstein gegründete Produktionsstätte, welche 1970 in Betrieb ging, ebenfalls hochinteressant. PV-Anlagen, die das gesamte Hallendach bedecken, erzielen rund ein Zehntel des gesamten Energiebedarfs im Werk durch Eigenproduktion. Zudem wird - dank zukunftsgerichteter Standortentwicklung – Erdwärme für die Gebäudetemperierung genutzt.
Aktuell sind die Gebäudeheizung und die Wärmebehandlung die versorgungskritischsten Prozesse, weshalb zusätzlich begonnen wurde Erdgas einzuspeichern. Darüber hinaus werden einige der Öfen in der Wärmebehandlung, beileibe nicht die letzten, bereits auf Strombetrieb umgerüstet. "Zusätzlich machen wir uns viele Gedanken zur Gasdiversifizierung, eine grundsätzliche Idee, "die wir mit der Installation von regenerativen Energien verbinden wollen", erzählt Christoph Holzer.
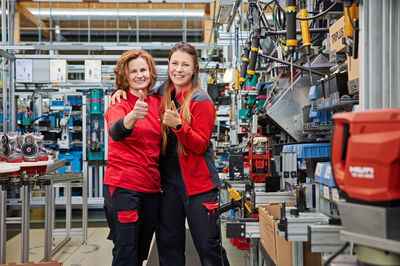
KATEGORIESIEG SMART FACTORY: NBG Fiber, Gmünd - Die smarten Prozessveredeler
Im Gmündner Glasfaser-Rohlingswerk von NBG Fiber können in Ausbaustufe Eins Preforms für 5,2 Millionen Faserkilometer erzeugt werden. Hoch digitalisiert - und mehr als awardwürdig.
Die Anreise zur Austragungsstätte von Fabrik2022 hoch oben im nordwestlichen Waldviertel fiel für drei Herren kurz aus - ein Spaziergang war der Weg ins Finale für Reinhard Apfelthaler (Leitung Instandhaltung), Christopher Brinnich (Produktionsplanung) und Christian Zwettler (CTO) freilich nicht.
Aber schon andere Herausforderungen wurden von den Niederösterreichern erfolgreich gestemmt: Tatsächlich findet sich vieles, was Big Player wie die Villacher Infineon auszeichnet, auch am NBG-Standort in Gmünd. Modernste Reinraumtechnologie etwa, aber auch hochgradig automatisierte Prozesse.
Das Werk, das die Niederösterreicher bei Österreichs härtestem Produktionswettbewerb ins Rennen schicken, ist hochmoderner Prägung: 2018 ließ das Team um Eigentümer Karl Bauer der Idee, über eine eigenständige GmbH europaexklusiv in die Produktion von Glasfaser-Preforms einzusteigen, rasch Taten folgen. Am Firmenareal in Gmünd wurde ein allen Ansprüchen gerecht werdendes Produktionswerk errichtet, das Anfang heurigen Jahres in den Regelbetrieb geschaltet worden ist.
6 Preformen pro Tag. Die Beherrschung des chemischen Prozesses, bei dem Maschinentechnologie der zur Knill Gruppe gehörenden finnischen Rosendahl Nextrom Einsatz findet, ist dabei alles andere als trivial. Die Rohlinge, rund 80 Kilo schwere, hochreine Glaskolben, wachsen bis 2.000 Grad und unter dem Einsatz chemischer Gase heran. Die Durchlaufzeit liegt bei 120 Stunden. In der 24 Meter hohen Produktionshalle bildet sich ein Kolben, aus dem später mehr als 2.500 Kilometer Glasfaser für den Datentransport gezogen werden können. Ziel und 100-prozentige Produktionskapazität ist die Fertigstellung von sechs fertigen Preformen pro Tag. "Wir sind aktuell im Ramp Up des Werkes und produzieren zwei fertige Preformen pro Tag", schildert Zwettler.
Digitaler Backbone. Die erforderlichen Prozessgase wie Helium, Sauerstoff aber auch Wasserstoff bezieht man von Air Liquide aus Schwechat. Den Betrieb der Gas- und Chemikalienversorgung verantwortet die Villacher Kinetics. Größtes Augenmerk liegt auf der Prozessparameterlandschaft, vom Einzelgewerk bis zur Abluft, die über Siemens-Technologie komplett digital abgebildet ist. Für das Sintern und Brennen braucht es Temperaturen bis 2.000 Grad, die Reinraumtemperatur muss bei konstant 22 Grad liegen. Das Werk ist nun auch für künftige Zeiten gut gerüstet. Man könnte das Gebäude - mit einem weiteren Investment - nämlich auch für das Ziehen von Glasfasern adaptieren. "Das wäre unser Zukunftsplan", sagt Zwettler.
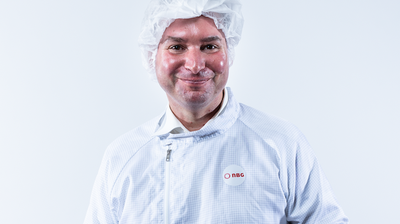
KATEGORIESIEG GREEN FACTORY: Europlast, Dellach im Drautal - Die nachhaltigen Effizienzmehrer
Zur Gänze klimaneutral produziert der Kunststoffbehälterhersteller Europlast, in Dellach im Drautal domiziliert. Das brachte den Kärntnern einen Kategoriesieg ein.
Die Oberkärntner, deren 140 Mitarbeiter als Teil der italienischen Jcoplastic-Gruppe zuletzt 45 Millionen Euro Umsatz erwirtschafteten, fertigen für die Abfallindustrie, Landwirtschaft und Logistik Dünnwand-Sammelbehälter aus Polyethylen hoher Dichte (HDPE). Und das ökologisch nachhaltig und auszeichnungswürdig: Der Anteil des eingesetzten Recyclingmaterials im Unternehmen liegt bei erstaunlichen 33 Prozent.
Genutzt wird Ökostrom, zum Teil aus der eigenen Fotovoltaikanlage. Reststoffe aus der ISO-50001-zertifizierten Produktion - man fertigt auf 15 Spritzgießmaschinen, die größten mit 4500 Tonnen Schließkraft versehen und damit schon dimensioniert wie Turnhallen - werden in den Prozess rückgeführt. Zusätzlich treibt das Unternehmen Kreislaufwirtschaftsprojekte voran: Kunden und Partner - einer ist der steirische Entsorger Saubermacher - animiere man, "ausgediente Behälter an uns zu übergeben", um daraus mit der hauseigenen, elaborierten Recyclinganlage durch Aufbereitung neue Behälter - Öko-Bins genannt - "zu fertigen", schildert Arthur Primus, CEO von Europlast.
Die Teilnahme bei der Fabrik2022 sollte dem Unternehmen wertvolle Impulse bringen, was gelungen ist. Und ja: natürlich sei man ziemlich stolz darauf, wie der Standort, für den es noch viele weitere Ideen für Optimierung und Effizienzsteigerung gibt, heute dasteht. Stichwort Weiterempfehlungsrate. Die liegt laut jüngster Kundenbefragung bei einhundert Prozent.
Von Groß- bis Kleinstserie. Nicht nur liegt man beim OEE-Wert in einem exklusiven Bereich, nämlich jenseits der 80-Prozent-Marke. Lose bis zu 50.000 Stück fertige man nach den Lean-Prinzipien, versehe diese nicht selten in nachfolgenden Prozesschritten auftragsbezogen für Kommunen in Kleinstserie nach besonderen Ausstattungs- oder Designvorgaben. Darunter das Rennerprodukt, den zwei- oder vierrädrigen Wertstoffsammelbehälter.
Exportiert wird in 28 Länder, vor allem stark nach Osteuropa, wo die Strukturen für geschlossene Entsorgungskreise "nachziehen", sagt Primus. Im Jahr produziert Europlast rund anderthalb Millionen Kunststoffteile. Ein potenzielles neues Geschäftsfeld haben die Kärntner auch schon identifiziert: Künftig wird man auch Wasserstofftank In-Liner aus PA für Lkw und Schiffe produzieren. Dies im wachsenden Geschäftsfeld Auftragsfertigung.
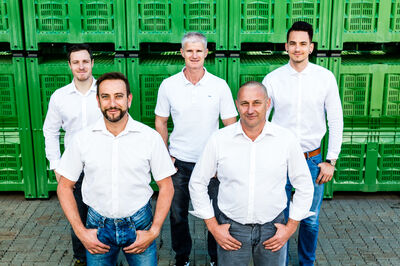
KPIs, bitte!
Weil KPIs mehr sagen als Worte: Die Spitzenwerte aus den Siegerfertigungen.
1,5 beträgt die KVP-Rate pro Mitarbeiter im Jahr bei Hilti in Thüringen.
100 Prozent Weiterempfehlungsrate weist die Oberkärntner Europlast auf.
250 Mitarbeiter wurden bei Siemens Mobility Austria im letzten Geschäftsjahr eingestellt.
5,2 Millionen Faserkilometer resultieren aus der Preforms-Produktion in Ausbaustufe Eins des NBG Fiber-Werks.
30 Maschinen fertigt Koenig & Bauer (AT) am Standort Mödling im Schnitt pro Jahr.
33 Prozent Prozent beträgt der Anteil an eingesetztem Recyclingmaterial bei Europlast.
80 Lehrlinge beschäftigt Hilti in Thüringen.
60 Tonnen CO2-Einsparung erreichte Siemens Mobility Austria durch die Umstellung auf E-Fahrzeuge und Routenzug.
6 sechs fertige Preformen pro Tag sind Ziel und 100-prozentige Produktionskapazität im Werk von NBG Fiber.
80 Prozent beträgt der OEE-Wert bei Europlast (24/7)
93 Prozent beträgt bei Hilti in Thüringen die Teilnahmequote bei GEOS, einer Umfrage zur Mitarbeiterzufriedenheit
3-mal höhere Flächenproduktivität durch Einsatz der digitalen Fabrik erzielte Siemens Mobility Austria.
33 Prozent Prozent beträgt der Anteil an eingesetztem Recyclingmaterial bei Europlast.
FINALIST: Siemens Mobility Austria, Wien - Die rasanten Lean-Umsetzer
Das komplette physische Maschinennetz der Siemens-Zugfertigung in Wien-Simmering ist virtuell gespiegelt. Ein steter Treiber: Die Lean-Philosphie.
In der Leberstraße 34 finden sich einige Superlative. Die Fertigungstiefe am Siemens-Mobility-Standort ist hoch, groß auch ist die Tradition des Werks mit seiner 175-jährigen Geschichte, in dem heute rund 1.400 Mitarbeiter in nicht weniger als 40 Hallen arbeiten. Montiert wird freilich in der gemeinsamen, 14.000 Quadratmeter-Halle im Fünfer-U-Zellen-Layout. Vom Rohau des Wagenkastens über das Schweißen und Oberflächenlackieren bis zur Montage - etwa dem Einsetzen von Fenstern und Haltestangen, aber auch der Elektrik sind hier alle Prozesse - inklusive Inbetriebsetzung - gebündelt. In der getakteten Fließfertigung - sechs Linien für den Rohbau, fünf Linien für die Montage - folgt man den Gesetzmäßigkeiten der Lean-Philosophie.
Erst kürzlich nahm man sich die Prozesse nochmals, neu betrachtet, zur Brust. "Wir krempelten so manches um, integrierten etwa weitere Prozessschritte wie Kleben oder das ISO-Prüfen", schildert Michasel Leisgang, der technischer Leiter. Natürlich jagt man auch Use-Cases aus dem Konzern in die eigenen Linienwelt. Was genau? Etwa das Auslastungsmanagement, die Feinterminplanung, Robotik oder Tools wie den Digitalen Produktzwilling. "Unser ganzes physisches Maschinennetzwerk ist mittlerweile im IT-Netz gespiegelt", sagt Leisgang. Die Nutzung der digitalen Fabrik bringe eine dreifach höhere Flächenproduktivität.
Nachhaltige Produktion. Auch bei der Nachhaltigkeit macht man Nägel mit Köpfen. Mittels 5.000 Quadratmeter großen PV-Flächen werden rund 1.000.000 Kilowattstunden Strom für den Eigenverbrauch erzeugt. Heizen durch Warmwasser rückt in den Fokus, es dient in der Hauptsache dazu, den Primärenergieträger durch Luftwärmepumpen oder Biogas "zu substituieren", schildert Sven-Oliver Fischer, der kaufmännische Leiter des Standorts. Auch sonst ist das Geschäft der Siemensianer dynamisch. Nightjet-Züge, ein wachsenden Segment und unlängst von der ÖBB für die Strecke Brüssel - Wien bestellt, sorgen hier in Simmering für Auslastung. Hochgeschwindigkeitszüge kommen aus dem Siemens-Werk Krefeld, Loks aus München, Drehgestelle aus Graz -Reisezugwägen und U-Bahnen, etwa für die Metro in London, dagegen aus Wien-11.
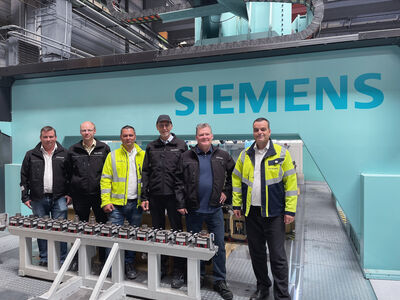
Finalist: Koenig & Bauer (AT), Mödling - Die tadellosen Taktfertiger
Das Mödlinger Druckmaschinenwerk unterzog sich einer radikalen Neuausrichtung seiner Produktionssystematik. Und hat damit erstaunliche Effizienzhebel in der Hand.
Ein radikaler Umbau des Werks, der gerade in die Zielgerade biegt, schlägt hier, in der Koenig & Bauer-Straße 2 in Maria Enzersdorf, positiv auf die Energiebilanz durch: Elf Prozent Effizienzplus soll eine zentrale Vormontage der drei Taktstraßen, die in einem von Grund auf neu konzipierten Hallenschiff an die Stelle der bisher in mehreren Hallen verteilten Vormontageinseln rückt, dem Maschinenbauer bringen. Nach einem kleinen baulichen Verzug liefen im Juli im Mödlinger Montagewerk für Wertpapiermaschinen die letzten Vorbereitungen vor der Zusammenfassung von Prozessen hierher. Schienensysteme, darunter eine kürzere Linie für den rund dreiwöchigen Zusammenbau kleinerer Aggregate, werden an ein- und derselben Linie größtmögliche Flexibilität bei der Montage von Druckwerken, Lackwerken und Aggregaten bieten. Taktweise wird von hier aus dann jeweils für den nächsten Morgen über Routenzüge in allen Montagen angeliefert.
Auf Kunden zugeschnitten
Acht von zehn Banknoten, die weltweit in Umlauf sind, werden auf Maschinen von Koenig & Bauer - einem Unternehmen mit über 200 Jahren Tradition - gedruckt. Mit 320 Mitarbeitern, rund 130 in der Montage, fertigt man in einem stabilen Kernmarkt - das Banknotengeschäft erweist sich als konstant - zwischen 20 und 30 Maschinen pro Jahr, von Einzelmaschinen bis hin zu verketteten Anlagen, wie sie einige Schlüsselmärkte gerade deutlich Zulauf erfahren. Wenngleich fast jede Maschine speziell auf Kunden zugeschnitten wird, wie es sich für den Sondermaschinenbau gehört, legt man bei der Effizienz Jahr für Jahr eine Schippe drauf.Ein Lehrlings-KVP führte zur Optimierung von Werkzeugwägen. Shadowboards - auch für Montageteile - "hielten im Werk Einzug", schildert Christian Kapper, der hiesige Montageleiter, seit 33 Jahren im Unternehmen tätig.
Automatisierungshilfen
Fortschritte visualisieren - wie hier in der Montagehalle Wertpapier 1 (WP1) - Tafeln auf Basis des Gemba-Walk-Prinzips. Zudem geben die SCRUM-Boards steckbriefartig Orientierung, welche Maßnahmen und Aktionen Mitarbeiter in einer Woche "hinsichtlich der Prozessverbesserung setzen", schildert Christoph Schefberger, Leiter der Montageplanung und Montagedisposition, der sich im Unternehmen des Lean-Themas angenommen hat. Auch das Retrofit-Geschäft läuft in Mödling rege. Eine - nagelneue - Super Orlof Intaglio - zeigt unterdessen, wie Automatisierung sich ihren Weg in die Produktwelt bahnt: Ein Montageroboter wird an dieser Maschine mit dem Griff in einen 100 Bögen fassenden Magazinspeicher Papier einlegen.
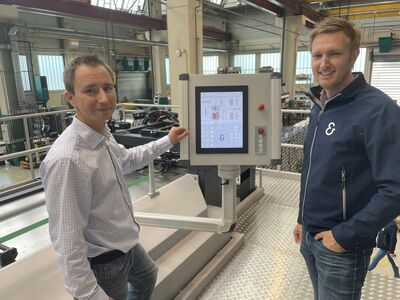
- #Nachhaltigkeit
- #Maschinenbau
- #Metallindustrie
- #Fabrikkonferenz
- #Coverstory
- #Siemens Mobility
- #Europlast
- #NBG Fiber
- #Hilti
- #Koenig & Bauer AT
- #Michasel Leisgang
- #Arthur Primus
- #Paul Scholz
- #Christian Zwettler
- #Christoph Schefberger
- #Sven-Oliver Fischer
- #Martin Rescher
- #Siegfried Hutter
- #Michael Pirker
- #Gerhard Schwarzenbacher
- #Michael Pritsch
- #Christopher Holzer
- #Christian Kapper