Kreislaufwirtschafts-Strategie in der Industrie : Der grüne Umbau der Industrie
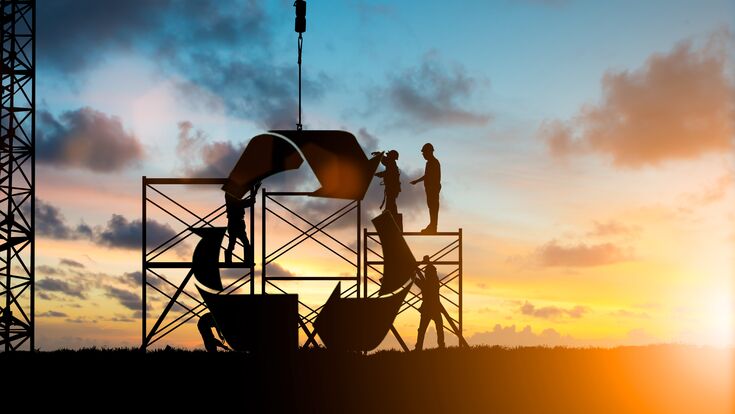
Der grüne Umbau der Industrie: Unternehmen setzen auf innovative Kreislaufwirtschaftsmodelle wie Faser-zu-Faser Recycling und Co-Processing in der Bauwirtschaft. Nachhaltigkeit wird bei Fronius durch langlebige und reparaturfreundliche Produkte gefördert.
- © Yuttana Studio - stock.adobe.comTextilrecycling ist ein Sorgenkind, denn die Wiederaufbereitung ist komplex. 85 % der weltweit produzierten Textilien landen auf Deponien oder werden laut Ellen MacArthur Foundation verbrannt. Gründe dafür sind die Materialvielfalt und die Fasermischung, die Farbstoffe, Bleichmittel und chemische Behandlungen, die im Herstellungsprozess verwendet werden. Diese führen auch zu dem Qualitätsverlust, der im Recyclingprozess, insbesondere bei synthetischen Fasern, das Gewebe oft unbrauchbar macht. Ein großer Durchbruch gelang der EREMA Tochter PURE LOOP. Mit der Entwicklung der neuen ISEC evo FibrePro:IV-Anlage ist das Recyceln von PET-Fasern und Geweben möglich geworden. Und zwar in einer Qualität, die aus dem entstandenen Regranulat erneut qualitativ hochwertige Fasern herstellt.
Nie mehr die wichtigsten News aus Österreichs Industrie verpassen? Abonnieren Sie unser Daily Briefing: Was in der Industrie wichtig wird. Täglich um 7 Uhr in Ihrer Inbox. Hier geht’s zur Anmeldung!
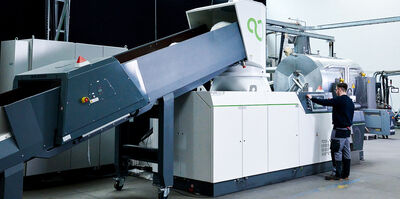
Recycling hat ein enormes Potenzial in der Faser- und Textilbranche, es wird in Zukunft zum Standard werden.Merlijn van Essen, Sales Manager bei PURE LOOP
Faser-zu-Faser Recycling durch Industrieabfall
Und so geht´s: Als Erstes werden die Faserabfälle aus Produktionsprozessen unzerkleinert in die Anlage eingebracht. Nach dem Shredder werden sie kontrolliert in einen Extruder geleitet und filtriert. Die entstandene Schmelze wird im IV-Uptimiser unter ständigem Rühren, in Kombination mit Vakuum und anschließender Verweildauer qualitativ verbessert. So werden Molekülketten erneuert und die intrinsische Viskosität gesteigert. Daher ist das gewonnene Regranulat wieder zu 100 % verspinnbar und kann ohne Zugabe von neuem Rohmaterial erneut zu Fasern verarbeitet werden.
>>>> Markus Comploj: Der letzte Textilfabrikant
In einem Pilotprojekt in Kooperation zwischen dem Sportbekleidungshersteller Sportstex, dem Kreislaufwirtschaftsspezialisten RadiciGroup und PURE LOOP wurde das erste gebrandete Trikot des Fahrradkomponentenherstellers Shimano produziert. Der zirkuläre Ansatz schont nicht nur die Umwelt, er birgt auch ein interessantes Geschäftsmodell. Die Faserproduktion steigt rasant, bis 2025 wird ein Anstieg bis 130 Millionen Tonnen erwartet. Allein aus den Produktionsabfällen der Branche ergibt sich ein Marktpotenzial von 40 Millionen Tonnen. "Recycling hat ein enormes Potenzial in der Faser- und Textilbranche, es wird in Zukunft zum Standard werden“, sagt Merlijn van Essen, Sales Manager bei PURE LOOP.
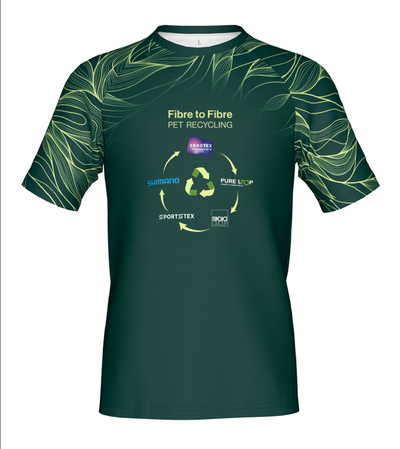
In Österreich allein verwenden wir jährlich rund 438.000 Tonnen Ersatzrohstoffe, davon entfallen 272.000 Tonnen auf Baurestmassen.Christian Lampl, Manager von Geocycle Central Europe
Co-Processing revolutioniert die Bauwirtschaft
Die Bauwirtschaft ist für 60 % des jährlich verbrauchten Rohstoffes verantwortlich, denn die Herstellung von Zement ist rohstoffintensiv. Was aber, wenn dieser große Bedarf an Rohstoffen mit Sekundärrohstoffen aus anderen Industrien gedeckt werden kann? Der eigentliche Nachteil verwandelt sich plötzlich in einen Vorteil. An dieser Schraube wird beim Zementhersteller Holcim und deren Tochter Geocycle mit Volldampf gedreht. „In Österreich allein verwenden wir jährlich rund 438.000 Tonnen Ersatzrohstoffe, davon entfallen 272.000 Tonnen auf Baurestmassen“, erklärt Christian Lampl, Manager von Geocycle Central Europe. Co-Processing heißt die Methode, die den Zaubertrick in der Herstellung von Sekundärrohstoffen vollführt. In diesem Verfahren ersetzt der mineralische Anteil des Abfalls primäre mineralische Stoffe wie Kalkstein, Ton oder Eisen und der brennbare Anteil liefert die für die Klinkerproduktion benötigte Energie. Durch hohe Temperaturen und lange Verweilzeiten in Zementöfen werden Abfallstoffe vollständig zerstört. Die Asche reagiert mit anderen Bestandteilen und bildet das Endprodukt.
>>>>> Die Lage am Rohstoffsektor: EU will sich Lieferketten sichern
So werden deponierbare Rückstände vermieden. Das Verfahren setzt auch Materialien, wie Schlacken aus der Stahlindustrie, Gießereisand und Verbundkunststoffe, die nicht recyclingfähig sind, ein. „Wir werden als Zementproduzenten auch zum Serviceanbieter für andere Industriezweige, indem wir Materialien, die oft auf der Deponie landen, verwerten und in unser Produkt einarbeiten“, freut sich der Geocycle Manager. 100 % der eingesetzten Abfälle werden recycelt und verwertet, ohne dass Rückstände anfallen. Vor allem in Infrastrukturprojekten, die einen großen Anteil an Roh- und Ausbruchsmaterialien haben, erweist sich die Einarbeitung in die Zementproduktion als Treiber für den Kreislauf, wie etwa beim Bau des Semmeringtunnels oder dem Bau der U5 in Wien.
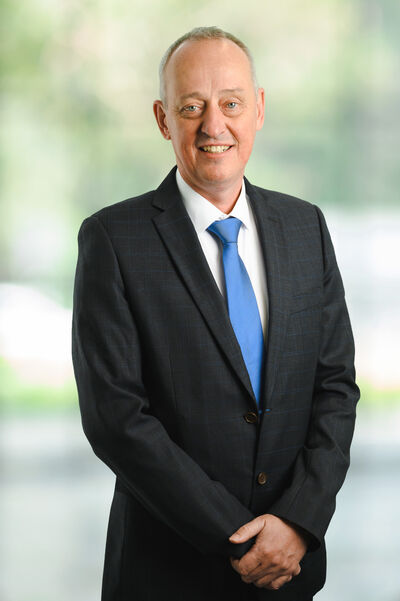
Wiederverwertbare Ziegelwände, innovativer Ansatz für nachhaltiges Bauen
Nicht alle Gebäude werden für eine Lebensdauer von 150 Jahren konzipiert. Vor allem die Gebäudenutzung der Verbrauchermärkte wird oft für nur 10 Jahre geplant, erklärt Mario Kubista, Leiter Produktmanagement Wand und Fassade beim Ziegelhersteller Wienerberger. Ziegel haben daher oft eine viel längere Lebensdauer als die meisten Gebäude. Dieser Aspekt ist die Grundlage für die Entwicklung eines nachhaltigen Gebäudessystems und die Erschließung neuer Geschäftsmodelle, die von der Ressourcenschonung profitieren können. Im Rahmen eines zweijährigen, von der Österreichischen Forschungsförderungsgesellschaft (FFG) unterstützten Projekts arbeitet ein Team unter der Leitung der Wienerberger AG, gemeinsam mit Partnern der TU-Graz und Wienerberger Österreich GmbH zusammen. Ziel ist, die Verschwendung funktionsfähiger Bauteile zu reduzieren und die Wiederverwertung in den Vordergrund zu stellen. „Wir wollen die Lebensdauer der Ziegel von der Lebensdauer des Gebäudes unabhängig machen“, so Kubista.
Die erste Herausforderung, die Erstellung von Fertigteilwänden, ist bereits gemeistert. Sie werden im eigenen Werk individuell geplant, vollautomatisiert vorgefertigt und können Geschosshoch aufgezogen werden. Die Montage auf der Baustelle bedarf dadurch weniger Personal, so verkürzt sich die Projektdauer, die Kosten sind niedriger und es entsteht weniger Bauschutt. Um diese Wände aber wieder verwenden zu können, bedarf es der Entwicklung von zerstörungsfrei lösbaren Verbindungen der Wände. Die Vorgabe ist, mechanische Befestigungen zu entwickeln, die einfach wieder lösbar sind. Tragwerk und Statik spielen in dabei eine Rolle, ebenso die Bauphysik, denn die Fugen zwischen den Elementen müssen luftdicht sein.
>>>> Wie CO2 plötzlich zum Rohstoff wird
Weitere Überlegungen gibt es zur Beschaffenheit und der Dicke des Verputzes, der auf dem Ziegelmauerwerk aufgetragen wird und einen einfachen Rückbau ermöglichen soll. Die Fertigteilwände sollen mindestens fünfmal wieder verwendbar sein. Der CO₂-Fußabdruck lässt sich somit drastisch reduzieren. Um diese Mehrfachnutzung zu gewährleisten, arbeitet das Forschungsteam außerdem an einer nicht invasiven Prüfmethode, die die Qualität dieser Weiternutzung gewährleisten kann.
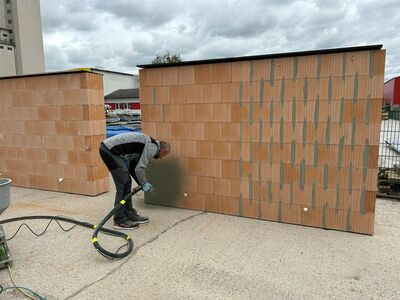
Nachhaltigkeit bei Fronius: Reparieren statt Wegwerfen
“Reparieren statt wegwerfen”, war bereits 1945 der Leitsatz von Günter Fronius, Gründer des Schweißgeräte, Antriebsbatterien und Solaranlagenherstellers Fronius. Der initiale Durchbruch gelang dem Unternehmen, als es als einer der Ersten im Stande war entladene Autobatterien wieder aufzuladen. Lebenszyklusanalysen und das Prinzip „Design für Sustainability“ sind Übersetzung der alten Leitsätze in die heutige Zeit. Die Umweltwirkung der Geräte wird in 13 verschiedenen Phasen ihres Lebenszyklus erhoben. Sie beinhalten die Rohstoffgewinnung, die Produktion, die Verwendung und die Reparatur bis hin zum End-Of-Life.
>>> AT&S, Fronius, Zumtobel: Die besten Unternehmen der Elektronik-Industrie
Das dadurch erlangte umfassende Wissen, über relevante Hotspots und Hebel im gesamten Produkteleben mündet in dem Drehen von Nachhaltigkeitschrauben und ist Basis für schnelle Reparaturen im Fronius Repair Center in Steinhaus bei Wels. 35.000 Serviceaufträge werden jährlich bearbeitet, dazu gehören die Reparatur und Wartung von Schweißgeräten, Solar-Wechselrichtern und Batterieladesystemen. Das Zentrum verfügt über ein spezialisiertes Team, das Servicekonzepte entwickelt, um sicherzustellen, dass die Geräte im Bedarfsfall instand gesetzt werden können. Dies umfasst sowohl die Reparatur von defekten Geräten als auch die Durchführung von Wartungsarbeiten, jährlichen Prüfungen und Kalibrierungen. Highlight der Bemühungen ist die Reparatur eines Schweißgeräts aus dem Jahr 1978.
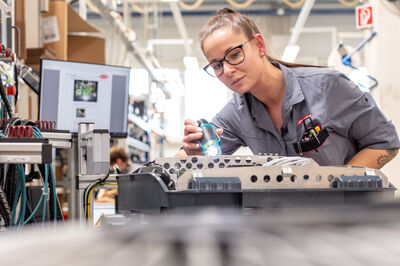