Effzienzprogramme : Wie Industriebetriebe jetzt ihre Produktion optimieren
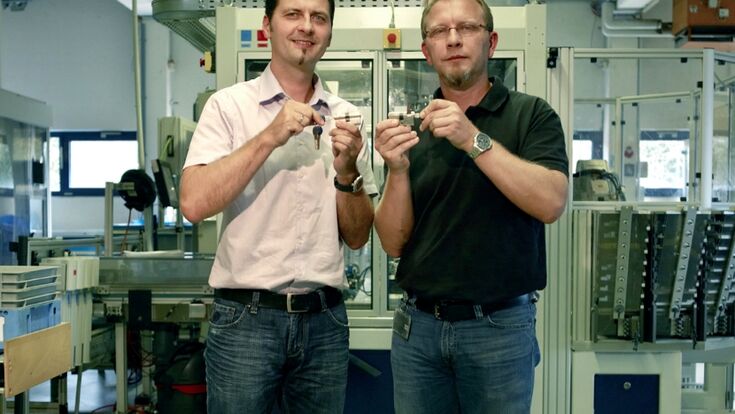
Besenrein. So präsentieren sich die Produktionshallen des Schließsystemeherstellers Kaba im niederösterreichischen Eggenburg. Der Boden blitzblank, jeder Arbeitsplatz aufgeräumt – sogar das Werkzeug hängt peinlich genau in den Sammelboxen. Doch das – ein Mitarbeiter nickt zustimmend – war nicht immer so. Erst 2009 habe man begonnen, sich “intensiv mit der Optimierung der Produktion auseinanderzusetzen“, bestätigt der örtliche Produktionsleiter, Christian Katona. "Auch in weniger guten Zeiten pochten Kunden auf extrem kurze Lieferzeiten”, begründet Christian Bruggraber, Produktionsleiter Eggenburg und Herzogenburg, den Schritt. Ein Trainerteam wurde auf die Beine gestellt. Und Themen wie Arbeitsplatzgestaltung und effizienteres Rüsten fanden in der Fertigung von Wendeschlüsselsystemen plötzlich Gehör. „Früher hatten wir sehr hohe Sicherheitsbestände“, sagt Christian Katona. Die habe man spektakulär "halbiert“, so Katona. Am eingeschlagenen Kurs halten die Niederösterreicher deshalb fest: "Auch kleinere Maßnahmen machten sich bisher voll bezahlt”. Auf und ab.Dem Aufschwung gehe langsam “die Puste aus“. So kommentierte Markit-Ökonom Tom Moore im Juli eine Umfrage seines Instituts unter knapp 1000 Unternehmen. Er macht dafür einerseits die schwächere Nachfrage nach Waren „made in Germany“ bei Handelspartnern wie den Euro-Ländern, China und den USA verantwortlich – aber auch die schlechtere Stimmung “wegen der Schuldenkrise”, so Moore. Mitbetroffen natürlich auch der Maschinenbau – hier verloren die Geschäfte zuletzt drastisch an Schwung. Der deutsche Auftragseingang war im Juli nur unwesentlich besser als im Vorjahr – doch es kam noch dicker: Das Inlandsgeschäft rutschte sogar um 14 Prozent ab, stellte der Verband Deutscher Maschinen- und Anlagenbau (VDMA) kürzlich wenig erbauliche Zahlen vor. Auch der der Ausblick ist trüb: Die Dynamik bei den Auftragseingängen dürfte sich im restlichen Jahr weiter “beruhigen”, formuliert es VDMA-Konjunkturexperte Olaf Wortmann höflich. Es gebe Anzeichen für ein “Einknicken” der Investitionsgüterkonjunktur, fand ein Forscherkollege deutlichere Worte. Wer schon jetzt gegen Produktionsverschwendungen vorgeht, “gehört später sicherlich zu den Gewinnern”, meint Berndt Jung, Chef von Six Sigma Austria. “Wer dauerhaft Verbesserungsprozesse ins Rollen bringt, ist auch in schwierigeren Zeiten auf der Überholspur”, meint Alexander Hrach, Trainer beim Kaizen Institute Austria. Befunde, die sich auch schon im letzten Abschwung bestätigten – panisches Gegensteuern kam hier meist zu spät. Viele Betriebe krempeln deshalb heute schon die Ärmel hoch – und durchlaufen auf die Fertigung zugeschnittene Optimierungsprogramme. INDUSTRIEMAGAZIN sah sich ganz unterschiedliche heimische Produktionen an – der Fortschritt in den Werken ist bei allen eindrucksvoll. Fortsetzung auf Seite 2: Mark Metallwarenfabrik - Produktionsdetektive auf heißer Spur.
In der Mark Metallwarenfabrik köcheln Optimierungsprojekte nicht auf Sparflamme. Die Oberösterreicher stellen Tiefziehteile her, die auch in die Autoindustrie gehen. Etwa zum Bremsanlagenbauer Conti. Für die Deutschen produziert Mark millionenfach Hülsen für Ventile, die etwa in Antiblockiersystemen Einsatz finden. In Stufenpressen entstehen zuerst die Rohlinge. Dann wird gestanzt, abschließend kontrolliert. Mehrere Waschprozesse begleiten das gut einstudierte Stück der 245 Mitarbeiter. Im Drehbuch stehen neuerdings aber auch zweimonatliche Qualitätsmeetings. „Denn kein Monat vergeht, in der die Autoindustrie nicht die Qualitätslatte anhebt“, berichtet Fertigungsleiter Johann Patz. Schon einmal wurde den Oberösterreichern die Rute ins Fenster gestellt. „Uns wurde gespiegelt, dass wir uns beim Thema Ordnung verbessern müssten“, schildert Patz. Der empörte Aufschrei in Spital am Pyhrn blieb darob aus: „Als Qualitätslieferant nahmen wir den Ball natürlich auf“, sieht er die Sache positiv. Und: Einen Kunden wie Conti darf man nicht verlieren.Ein gutes Jahr liegt der wohlmeinende Tadel nun zurück – seither hat sich bei den Oberösterreichern viel getan. Die Werkbänke wurden übersichtlicher. Fürs Handwerkzeug definierte man fixe Aufbewahrungsorte. Und die Werkzeuglagerung im Bereich der Stufenpressen ist nicht mehr chaotisch. Schlecht beschriftete Ziehmatrizen und Stempel mussten die Mitarbeiter früher aus winzigen Behältern kramen. Eine kleine Investition in Schwerlastschränke mit Ladefugen brachte es voll. "Es sind jetzt sehr schöne Unterteilungen möglich“, sagt Patz. Die Suchzeiten reduzierten sich damit dramatisch. Und auch der schonendere Umgang mit dem Werkzeug war „ein erwünschter Effekt“, sagt der Fertigungsleiter.Die „Detektivarbeit“, wie Patz die Fehlerreduktion im Hause bezeichnet, geht jetzt in die Verlängerung. Denn erst vor wenigen Wochen fand es der Qualitätsleiter eines Autozulieferers der Mühe wert, „uns aufs Thema Nullfehlerproduktion anzusprechen“, schildert Patz. Die Oberösterreicher liegen derzeit bei zwei bis sechs Schlechtteilen pro Million Teile – kein schlechter Wert. „Es geht aber noch besser“, ist Patz überzeugt. Zwar sei die Produktion schon „ziemlich durchoptimiert“. Doch ein Angriffspunkt seien vielleicht die Prüfmaschinen. „Ihre Feinjustierung ist eine Wissenschaft“, so Patz. Fortsetzung auf Seite 3: W & H Dentalwerk Bürmoos - Puffer für Rennerprodukte
„Es ging uns vielleicht zu gut“. Johann Fersterer, Betriebsleiter beim Hersteller zahnmedizinischer Präzisionsgeräte W & H, bringt die frühere Stimmungslage auf den Punkt. Schon 2002 nahm der Betrieb in Bürmoos Projekte für mehr Ordnung in der Produktion in Angriff. Und wie es sich gehört, wurde dafür ein ehrgeiziges Ziel formuliert: „Das Rüsten unserer Bearbeitungszentren sollte nur mehr durchschnittlich eine Stunde dauern“, erzählt Fersterer. Bloß: Die Umsetzung war halbherzig. Die Projekte hatten Beibootcharakter. „Wir ließen sie nebenherlaufen, anderes war wichtiger“, räumt der Produktionsprofi ein. Von solchen Aktionen hat man sich längst verabschiedet. Bis Jahresende wird der Betrieb 34 seiner 300 Mitarbeiter in der Produktion zu Kaizen-Praktikern ausgebildet haben. Und einige schöne Projekte trieb das Unternehmen schon mit Schwung voran. Eins betrifft die rund 100 Bearbeitungszentren. Sie sollen – so das Ziel – effizienter gerüstet werden. Auf den Maschinen wird gebohrt und gefräst – damit sind sie der Geburtshelfer für 5000 Artikel in mehreren Segmenten wie Restauration, Prothetik oder Oralchirurgie. Früher verschlang das Rüsten massiv Zeit – im Schnitt vier Stunden pro Maschine. „Heute liegen wir bei 42 Minuten“, rechnet Walter Annegg, der Kaizen-Manager des Betriebs, vor. Doch wie ließ sich eine solche Verbesserung erzielen? Viel Hirnarbeit und Herzblut brachten die Mitarbeiter auf, soviel ist klar. Auf drei typischen Maschinen der Marken Traub, Benzinger und Deco experimentierten sie wochenlang mit der optimalen Teile- und Werkzeugbelegung – bis “einfach alles zusammenpasste”, so Annegg.Reduziert wurde auch die Rüsthäufigkeit. Große Eingriffe – etwa bei unterschiedlichen Durchmessern oder dem Wechsel von Buntmetall auf Stahl – wurden dezimiert. „Wir müssen jetzt seltener die Stangenführung umbauen“, freut sich Betriebsleiter Johann Fersterer. Und statistische Ausreißer – also rüstintensive Teilefamilien – hat man schonungslos enttarnt. Wir können sie jederzeit „an die verlängerte Werkbank abgeben“, so Fersterer.In der Zielgeraden liegt auch das zweite Projekt der Salzburger. Es ist in der Endmontage zahnärztlicher Winkelstücke angesiedelt – „und hält uns ganz schön auf Trab“, schildert Kaizen-Manager Walter Annegg. Die Salzburger versuchen hier, einen Produktionspuffer aufzubauen. Rennerprodukte – nicht nur im Segment der Winkelstücke – „wollen wir künftig schon vormontiert auf Vorrat halten“, erklärt Annegg. Damit will der Betrieb die “großen Nachfragesprünge abmildern“, ergänzt Betriebsleiter Johann Fersterer. Das dürfte funktionieren. Bei den Winkelstücken fehlt nur mehr die Beschriftung, etwa die Seriennummer. Riesige Bestände will der Betrieb aber nicht aufbauen. „Die Komponenten sollen nicht maximal drei Tage auf Lager liegen”, betont der Produktionsmanager. Fortsetzung auf Seite 4: AHT Cooling Systems: Schwenk an der Gitterbox
Die Einführung eines Produktionssystems ist an sich schon ein Riesending. Doch beim steirischen Tiefkühltruhenhersteller AHT wollte man mehr. 2010 führte der Betrieb sein Produktionssystem ein – gleichzeitig „vertieften wir uns in die Prinzipien der schlanken Fertigung“, erzählt Technikchef Uwe Klossowski. Die Typenvielfalt sei „explodiert“, begründet der Manager den Schritt. Zugleich wollte man in wirtschaftlich schwierigem Umfeld weiter bestehen. Berater im klassischen Sinne hatten bei Klossowskis Vorhaben keine Chance. „Wir wollten von vornherein Arbeitskreise, um die Motivation beim Team hochzuhalten“, erzählt der Manager des Rottenmanner Betriebs. Die Wahl fiel auf einen heimischen Trainingsanbieter. Heute – das zeigen die Montagehallen der Steirer eindringlich – sind die Fortschritte beachtlich. Verbesserungen finden praktisch permanent auf allen vier Montagelinien für Supermarktttruhen, Eiscremetruhen und Getränkekühler statt. Ein Riesenthema war Sauberkeit und Ordnung. „Wir zergliederten unsere Fertigung deshalb in 38 Bereiche“, erklärt Philipp Hartl, Koordinator des Produktionssystems. Neben Dingen, die die tägliche Arbeit erleichtern – etwa Bodenmarkierungen für mehr Übersicht –, brachte man auch Ordnung in die Beschaffung von Hilfsstoffen und Betriebsmitteln. Bei Spritzgusswerkzeugen kaufte der Betrieb früher sechs verschiedene Anschlusskupplungstypen nach – „jetzt sind es nur mehr zwei“, so Hartl. Damit tritt der Betrieb nicht nur in der Beschaffung anders auf. „Auch die interne Bevorratung ist wesentlich einfacher geworden“, sagt Hartl. Leichter tun sich auch die Betriebselektriker. „Früher gab es an den Arbeitstischen eine Vielzahl unterschiedlicher Anschlüsse – „für den Elektriker ein Horror“, meint Hartl. Nun at der Betrieb “einheitliche Standards” für die Verkabelung durchgesetzt.Der Betrieb verbesserte auch den Produktionsfluss. In der Aggregatmontage – einem Herzstück der Rottenmanner Fertigung – konnte die Produktionsfläche um ein gutes Viertel verkleinert werden. Als Zwischenpuffer nutzt man Gitterboxen – “früher waren es 155, jetzt sind es fünf”, erzählt Hartl. Auch einzelne Handgriffe sind für die Arbeiter leichter geworden. Früher mussten sie die schweren Kompressoren per 180-Grad-Schwenk von der Palette hanteln. „Jetzt führen wir die Bauteile vorne zu", schildert Hartl. Ein Riesenschub gelang nicht zuletzt auch in Sachen Qualität. „Mängel beseitigen wir seither effizienter”, erzählt Technikchef Uwe Klossowski. Die wöchentlichen Qualitätsbesprechungen sind dabei ein nicht zu unterschätzender Faktor. Und das Kennzahlensystem, das noch ganz frisch ist. Vollautomatisch per Computer erfasst, "studieren wir täglich die Nacharbeitsquoten und leiten daraus Korrekturmaßnahmen ab“, so Produktionsexperte Philipp Hartl. Fortsetzung auf Seite 5: Kaba - Optimierungsgremium als Schlüssel
1500 Quadratmeter Produktionsfläche nennt der Schließsystemehersteller Kaba in Eggenburg sein eigen. “Unzählige Varianten von Wendeschlüsselsystemen fertigen wir hier”, schildert Produktionsleiter Christian Katona. Der kontinuierliche Verbesserungsprozess nimmt – auch angesichts des wirtschaftlichen Drucks – dabei eine besondere Rolle ein. „Früher gab es dafür Briefkastensysteme” erzählt Katona. Die bewährten sich aber weniger. Es kamen gute Inputs, aber nur selten „lag der Fokus wirklich auf der Produktion“, erinnert er sich. Mittlerweile läuft das Vorschlagswesen über ein Gremium, in dem sämtliche Produktionsoptimierer vertreten sind: “Abteilungsleiter, Meister, aber auch Vorarbeiter”, schildert Katona. Und zweimal jährlich stattfindende Audits mit dem Schwesternstandort in der Schweiz machen die Zusammenarbeit intensiver – “wie auch Videokonferenzen“, erzählt Christian Bruggraber, Produktionsleiter Eggenburg und Herzogenburg. So tauschte man sich standortübergreifend beim Thema Rüsten aus. Die Workshops waren ein “Riesenerfolg”, sagt Christian Katona. Er veranschaulicht dies anhand einer Zylinderbohrmaschine. Alle Schraubenschlüssel sind neuerdings ordentlich in der Werkzeugsammelstelle abgelegt. Zugleich erhöhten die Niederösterreicher die Lebensdauer der Spindel. "Wir sattelten auf kürzere Handwerkzeuge um, um weniger Drehmoment zu erzeugen“, erklärt Katona. Auch einen Ausblick verwehrt er seinen Besuchern nicht. Die Niederösterreicher stellen gerade ein neues Kennzahlensystem auf die Beine. Katona: "Gängige Modelle sind häufig unscharf“. Was so gar nicht zur besenreinen Fertigung der Eggenburger passen will. Daniel Pohselt