EU-Regulierung : Umstrittener Energiesparzwang für Werkzeugmaschinen
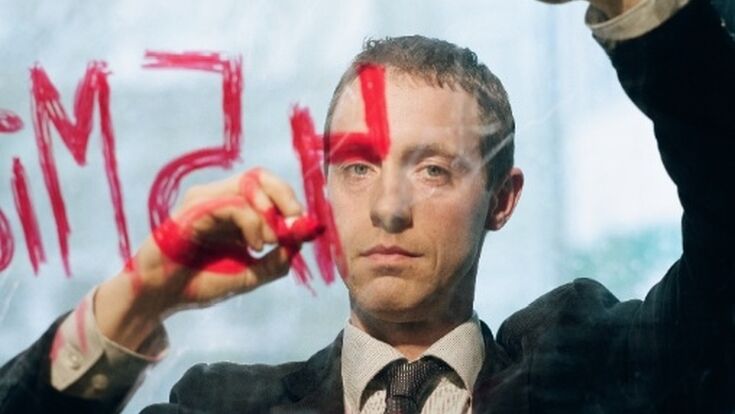
Es lag etwas in der Luft – und ein fröhlicher Frühlingshauch war es an diesem Donnerstag mit Sicherheit nicht. Denn um die Fortschritte der Fraunhofer-Arbeitsgruppe galant zu überspringen und sich dem schönen Wetter zuzuwenden, dafür waren die Vertreter der europäischen Maschinenverbände Ende März nicht nach Brüssel gereist. Bei diesem zweiten Stakeholder-Meeting ging es ans Eingemachte. Die von der EU-Kommission mit der Studiendurchführung beauftragten Berliner Institute (siehe Kasten) präsentierten weitere Details, wie die Umsetzung der europäischen Ökodesign-Richtlinie – nach Glühbirnen oder Elektroantrieben – nun auch bei Werkzeugmaschinen ohne Bruchlandung gelingen könnte. Mehr als zwei Jahre – noch bis Mai 2012 – nehmen sich die deutschen Auftragsforscher Zeit, Energieverbrauche und sich daraus ergebende Einsparpotentiale bei Industriemaschinen aufzudecken. Die Resultate könnten die Basis eines Rechsetzungsprozesses durch die EU sein – sprich, schon Grundlage für verpflichtende Effizienzanforderungen beim Bau einer Maschine sein. Schon jetzt ist die in sieben Kapitel unterteilte Vorstudie der Berliner mehrere hundert Seiten stark. Weniger angreifbar wird sie damit nicht. Der Verein Deutscher Werkzeugmaschinenfabriken VDW zerpflückte als einer der ersten die Methoden und Zwischenergebnisse der Forscher. „Einige Schritte sind keineswegs nachvollziehbar“, sagt auch Martin Baminger, Referent beim heimischen Fachverband Maschinen & Metallwaren Industrie (FMMI). Er war dabei, als es in Brüssel Ende März etwas lauter wurde. Die Industrieseite sei von der offensichtlichen Nonchalance der Forscher genervt gewesen, „erst falsche Schlüsse zu ziehen und es hinterher herunterzuspielen“. Selbstregulierung als Hoffnungspfad. Mit der sogenannten MEEuP(European Commission Methodology for Ecodesign of Energy-using Products)-Methode versuchen die europäischen Ordnungshüter, den Energiespargedanken auf möglichst viele Seiten auszuwalzen. Dass es früher oder später auch Werkzeugmaschinen treffen könnte, war absehbar. Der Energiebedarf aller metallverarbeitenden Maschinen in der EU wird von Fraunhofer mit jährlich 210 bis 320 Terawattstunden geschätzt – das stellt ein schönes Einsparpotential in Aussicht. Schon 2008 zeichnete sich ab, dass Werkzeugmaschinen ein möglicher Kandidat für eine Verordnung sind. Das europäische Komitee für die Zusammenarbeit der Werkzeugmaschinenindustrien in Brüssel, kurz CECIMO, brachte daraufhin eilends einen Antrag auf „Selbstregulierung“ ein – und hofft bis heute, mit einer selber erstellten Studie durchzukommen. Auch, weil schon länger Arbeiten an einer Norm im Gange sind. Die ISO 14955 soll den Weg für eine energieeffiziente Auslegung und Gestaltung von Werkzeugmaschinen ebnen. Doch die Chancen auf Selbstregulierung – das war bald Gewissheit – sind seither nicht unbedingt gestiegen. Denn nur wenige Wochen später schrieb die Kommission die Durchführung einer unabhängigen Studie aus – und Fraunhofer kam zum Zug. „Steuerverschwendung“, murrten einige. Jetzt läuft die Bedarfserhebung auf Hochtouren – den Gegenwind seitens der Industrie haben die Forscher aber „offenbar unterschätzt“, meint ein Branchenkenner. Denn kürzlich wurde publik, dass die Laufzeit der Studie um weitere Monate auf Mai 2012 verlängert wird. Von der Spindel über die Steuerung bis zum Maschinenbett: Fünf repräsentative Maschinentypen – unter anderem eine Biegemaschine sowie eine vierachsige Fräsmaschine – werden gerade auf ihr energetisches Verhalten untersucht. „Die Befürchtung, dass hier falsche Schlüsse für die schiere Masse an verfügbaren Maschinentypen gezogen werden, liegt nahe“, sagt Timo Würz, stellvertretender Chef und Technikleiter des Vereins Deutscher Werkzeugmaschinenfabriken VDW. Die Consulter hätten sich bisher nicht als „übermäßig kompetent“ in der Durchführung der Studie erwiesen, kritisiert Würz. Fortsetzung auf Seite 2.
Für die Maschinenbauerverbände, die eine schützende Hand um ihre Klientel legen, ist die Sache klar: Die Regulierungswut der EU würde den Aufwand der Maschinenbauer in die Höhe treiben, wenn plötzlich sparsamere, aber in der Anschaffung teurere Komponenten verbaut werden müssten. Das wäre aber noch das kleinere Übel. Zu befürchten ist laut Martin Baminger vom FMMI, dass nicht nur Hersteller weniger energieeffizienter Maschinen zu einer Aufholjagd verdonnert würden. Die bisherige Methodik der Studie ließe die bequeme Möglichkeit offen, eine „prozentuelle Verbesserung für alle“ vorzuschreiben. „Bei Herstellern mit sehr sparsamen Maschinen wäre der Aufwand, ein paar zusätzliche Prozentpunkte aus ihren Maschinen zu quetschen, dann ungleich höher“, sagt Baminger. Energieeffizienz sei außerdem kein neuer Trend, sondern längst nötig, meint er. Viele Maßnahmen seien „längst schon umgesetzt“, meint auch Timo Würz vom VDW. Und: Einige Schritte zu sparsameren Maschinen – etwa die Energierückspeisung – habe die Industrie „nie an die große Glocke gehängt “. Dass die Kommission die Werkzeugmaschinen ungeschoren lässt, hält Würz für unwahrscheinlich: „Der politische Wille zur Regelung ist groß“, sagt er. Die Fronten verhärten sich. Nicht erstaunlich also, dass die Verbände schon die ersten Kapitel der Studie zum Anlass nahmen, schwere Geschütze aufzufahren. „Metallverarbeitungsmaschinen, Holzbearbeitungsmaschinen, Teile von Kunststoffverarbeitungsmaschinen – es wird alles in einen Topf geworfen“, bemängelt etwa Martin Baminger vom FMMI an der Vorstudie. Der Geltungsbereich der Studie „wurde eindeutig zu weit gefasst“, sagt auch Timo Würz vom VDW. Tatsächlich sind Fräsmaschinen, Abkantpressen, aber auch Schweißgeräte mit dabei – ausgeklammert wurden etwa tragbare Kleinstmaschinen oder „komplette Kunststoffmaschinen“, weiß Würz. Umfrageergebnisse weckt Kritiker. Aber auch an anderer Stelle hagelt es Kritik. Um den Energiebedarf von Maschinen hochzurechnen, erhoben die Studienautoren zunächst die Zahl installierter Maschinen in der EU 27. Die Forscher kamen auf 33 Millionen Maschinen. Ein Wert, der Martin Baminger vom FMMI gleich „seltsam erschien“. Mittlerweile griffen die Studienautoren korrigierend ein. Die neue Annahme: 4,5 Millionen installierte Maschinen. Blutdrucksteigend wirkte sich für die Industrievertreter auch eine Umfrage aus, deren Ergebnisse in der Studie veröffentlicht sind. Die Befragung von neun Unternehmen kommt zum Ergebnis, dass Maschinenkäufer das Kapitel Energieeffizienz als wenig wichtig erachten. „Ein furchtbares Argument für uns“, meint Martin Baminger vom FMMI. Denn es lege den Schluss nahe, dass wir die „Regulierung unbedingt brauchen“, sagt er. Die Meinungen darüber gehen freilich auseinander. Clemens Pörnbacher, F&E-Leiter von Emco, etwa meint, dass die Kaufmotivation des Kunden letztlich doch stark vom Preistaferl abhängig sei. „Welche Kosten die Maschine in zwei Jahren verursacht, interessiert hingegen nur die wenigsten“, sagt er. Fortsetzung auf Seite 3.
„Viel Aufwand für wenig Geld“, so beschreibt Benjamin Kuhrke, Benjamin Kuhrke, Werkzeugmaschinenprofi an der TU Darmstadt, die Aufgabe der Fraunhofer-Kollegen. Damit liefert er noch das profanste Argument. Das Risiko, sich der Diskussion mit der Industrie stellen zu müssen, ohne eine konkrete Vorstellung zu haben, wie ordnungsrechtliche Maßnahmen zur Verbesserung der Energieeffizienz für das breite Spektrum von Werkzeugmaschinen ausgestaltet sein könnten, würde er persönlich „nicht eingehen“ wollen. Und die Kritik der Verbände an den Auftragsforschern hält an. Mit der Auswahl der fünf Testfälle ist CECIMO nicht ganz glücklich. Weniger an der Auswahl selbst stößt man sich. „Ein Vierachs-Fräszentrum ist durchaus repräsentativ, es ist in der Praxis oft zu finden“, meint etwa Timo Würz vom VDW. Aber es missfällt die Art und Weise, wie die Forscher zu den Einzelfällen gekommen sind. Im Fall der Fräsmaschine sei mithilfe von neun Beispielen für Bearbeitungszentren „einfach der Mittelwert errechnet“ worden, kritisiert Würz. Er weiß es deshalb so genau, weil die Beispiele unter anderem vom Verband selber kommen. Auch mit dem Vorschlag, für die Energiemessung die in der Geräuschmessnorm ISO 8525 definierten Betriebszustände zu verwenden, machten sich die Auftragsforscher keine Freunde. Würz: „Das ist Unsinn – aber wir können uns den Mund fusselig reden“. Leichtbau für alle?Sieben Module – das Gehäuse, Führungen und Lager, Antriebe, Steuerungs- und Hydraulikeinheiten, Pneumatik, Prozessmedienanlieferung sowie Energieversorgung – sehen sich die Forscher im Detail an. Eine Erkenntnis hat sich schon breit gemacht. Nicht beim Bau der Maschine, sondern in der Nutzungsphase geht am meisten Energie drauf. In den fünf Testszenarien werden in einem zweiten Schritt die besten verfügbaren Technologien Berücksichtigung finden. „Eine ganze Latte von Maßnahmen sei angeführt“, weiß Timo Würz vom VDW. Das liest sich so: Hydraulik- und pneumatikoptimierte Systeme: Bis zu 66 Prozent Energieeinsparung. Energiemanagement: 23 Prozent Energieersparnis im Dreischichtbetrieb. „Leider wurden hier teils wieder falsche Schlüsse gezogen“, meint Timo Würz. Dass der Leichtbau eine einfache, kostengünstig umsetzbare Maßnahme sei, ist einfach nicht richtig“, kritisiert Würz einen Passus der Fraunhofer-Vorstudie. „Leichtbauspannmittel sind unmöglich für alle Maschinentypen zu realisieren“, bestätigt auch ein Werkzeugmaschinenexperte. Auch die Begeisterung, die die Studienautoren für drehzahlgeregelte Pumpen zeigen, bereitet Timo Würz vom VDW Sorgen: Deren Vorzüge ließen sich in der Metallverarbeitung nicht so einfach verallgemeinern oder gar „in Prozent ausdrücken“, so Würz. Effizientere Klimageräte. Freilich: Bis dato gibt es keine ausdrückliche Empfehlung für eine der Technologien, es handelt sich dabei mehr um eine Auflistung brauchbarer Ansätze. Eine ist das Energiemanagement zur bedarfsgerechten Ansteuerung von Komponenten oder zur automatischen Abschaltung mittels Maschinensoftware. Hier ortet auch TU Darmstadt-Forscher Benjamin Kuhrke im Falle einer gesetzlichen Regelung am ehesten Potential für eine verpflichtende Maßnahme seitens der EU. Hauptspindel und Vorschubantriebe seien schon weitgehend ausgereizt. „Rückspeisefähige Umrichter werden schon von nahezu allen Herstellern eingesetzt“, meint Kuhrke. Und effizientere Standard-Asynchronmotoren oder Ventilatoren wurden von der EU bereits zwangsverordnet. Nun könnten auch effizientere Kompressoren – man kennt sie aus Schaltschrankklimageräten – eingesetzt werden. Ein Szenario, dass Kuhrke zumindest als „nicht unrealistisch“ bezeichnet. Teuerungsschub wird befürchtet. Und wie reagieren die Maschinenbauer beim möglichen Ausblick auf höhere interne Kosten, zusätzliche Entwicklungsarbeit und verdrossene Kunden wegen teuerer Maschinen? Wegen der “derzeit kritischen Situation” bei der Erstellung der Durchführungsmaßnahmen zur Ökodesign-Richtlinie will ein großer Maschinenbauer lieber schweigen. Andere sind ziemlich aufgebracht, weil sie jahrelang Energie in ihr eigenes grünes Label gesteckt haben. Mit Maschinenmesswerten für ihre Studie unterstützt die deutschen Forscher auch der Halleiner Werkzeugmaschinenbauer Emco nicht. Steigende Kosten seien durchaus „eine Sorge“, meint F&E-Leiter Clemens Pörnbacher. Ein Grund, weshalb die Salzburger ihre Maschinen mit Elektrospannzylinder statt permanent laufenden hydraulischen Pumpen nur „auf Anfrage“ anbieten, erzählt Pörnbacher. Das bessere Spannmittel schlägt mit rund 9000 Euro zu Buche – „als fixer Bestandteil würde das beim Neukauf abschrecken“, glaubt er. Das größte Energieeinsparpotential sei seiner Meinung nach beim Grundbedarf der Maschine – also bei eingeschalteten Antrieben und in Regelung – zu heben, ist Pörnbacher überzeugt. Ein Thema, dass die Salzburger derzeit schon in einem FFG-Projekt beackern. „Das Glück wird den bevorzugen, der schon jetzt handelt“, wappnen sich die Salzburger schon heute für ein mögliches verpflichtendes Regelwerk durch Brüssel. Das könnte es laut Experten frühestens 2015 geben. „Gute Durchmischung“.Der Sondermaschinenbauer Fill rechnet Kunden schon heute die Kosten eines Bearbeitungsschritts bis zum letzten Cent vor. Somit liegt der Schluss nahe, dass auch die Oberösterreicher mit dem EU-Vorhaben etwas anfangen können. Harald Sehrschön, Teamleiter Produktentwicklung, war beim ersten Stakeholder-Treffen dabei. Auch über den Letztstand ist er im Bild. „Es scheint sich eine gute Durchmischung aus wirklich sinnvollen Maßnahmen anzubahnen“, meint er. Jedoch hadere er auch etwas damit, dass die Ausfallssicherheit der Maschine nicht berücksichtigt werde. Denn die senke auch den Energieaufwand. Auch Standardmaschinenbauer müssen unter Umständen bald mit effizienteren Maschinen nachlegen. Eine Entwicklung, die nach Meinung von Roland Haas, Technischer Leiter von Anger Machining, nicht seine unmittelbare Konkurrenz stärken würde. „Große Maschinen wie unsere Bearbeitungszentren werden immer effizienter sein als kleine“, hält er nichts von bangen Blicken in die Zukunft. „Längst nicht alle Mitglieder des VDW sehen das mögliche Regulierungsvorhaben so verbissen wie der VDW selbst“, ist einem Branchenkenner aufgefallen. Klar ist: Die europäischen Verbände werden die Fortschritte der Fraunhofer-Arbeitsgruppe in Meetings auch weiterhin nicht galant überspringen. Daniel Pohselt