Lagerlogistik : Platz da! Die effizientesten Lager Österreichs
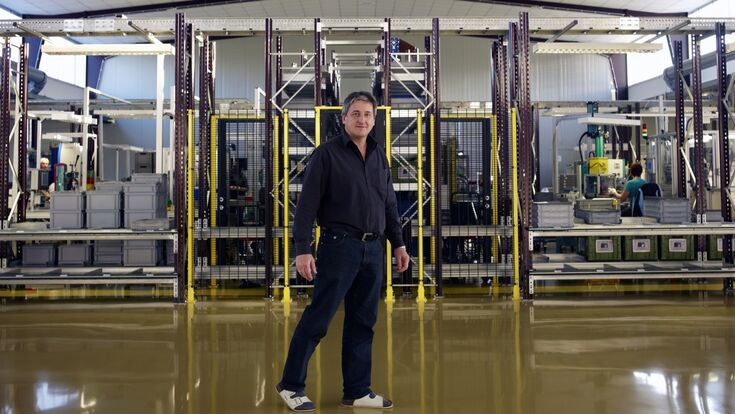
Ewald Lampl brauchte dringend mehr Durchblick. „Wir hatten Paletten mit Teilen rund um die Arbeitsplätze herumstehen.“ Was auch bei den zumeist kleinen Losgrößen, die der Betriebsleiter des Automobilzulieferers MSG Mechatronic Systems im steirischen Wies zu verantworten hat, eine Menge Platz und Nerven raubte. Also entwickelten Geschäftsführer Hans-Jörg Gasser und Lampl mit dem Logistik-Automatisierer Ylog kurzerhand ein völlig neues Lagerkonzept: Lager und Produktion wurden in einer Halle zusammengeführt. Die Integration in die Fertigung wurde 2010 umgesetzt, als MSG an einen größeren Standort übersiedelte. Von einer in der Mitte der neuen Halle angesiedelten Lagerfläche versorgt jetzt ein frei fahrendes Shuttle jeden der an den Längsseiten der Halle aufgefädelten Arbeitsplätze mit genau den Teilen, die der Assembling-Mitarbeiter für die aktuell gefertigte Baugruppe braucht, lagert halbfertige Baugruppen ein und später fertige zum Versand aus. Außerdem übernimmt es den Transport halbfertiger Baugruppen von einer Maschine zur anderen und dient damit als fahrendes Zwischenlager. MSG: Zwischenlager auf RädernDie Vorteile liegen für Betriebsleiter Lampl auf der Hand: „Früher haben wir jede Teilekiste, jede Palette mit dem Hubstapler aus dem Lager holen müssen – diesen Weg ersparen wir uns jetzt.“ Was auch wegen mancher Kundenvorgaben wichtig ist –MSG produziert unter anderem Ventile, die in staubarmer Umgebung gefertigt werden. Die Stapler brachten früher im Hin und Her zwischen penibel gefegter Fertigung und staubigem Kleinteilelager einigen Schmutz mit. Diese Fehlerquelle fällt jetzt weg, weil keine Hubstapler mehr durch die Gegend fahren, sondern nur noch das Shuttle in den Gassen des Lagerteils. Der kleine Flitzer bekommt seine Arbeitsaufträge über Bedienerterminals in der Nähe der Fertigungsplätze und im Auslieferungslager und ist kabellos über WLAN angebunden. Die Ylog-Programmierer tüfteln schon am nächsten Schritt: Ab 2012 sollen Barcode-Scanner die manuelle Tippeingabe an den Terminals ersetzen.Das von Ylog entwickelte 50 Kilo leichte „Autonomous Intelligent Vehicle“, das bei MSG im Einsatz ist, entspricht dem Kompakttrend in heimischen Lagern. Wendigkeit ist Pflicht: „Alle vier Räder sind um 90 Grad schwenkbar, ein Shuttle kann daher alle Längs- und Quergassen erreichen“, beschreibt Ylog-Geschäftsführer Heinrich Amminger die Selbstfahrer. Weil sie kein vorderes und hinteres, oberes und unteres Anfahrtsmaß benötigen wie herkömmliche Regalbediengeräte, lässt sich das Lager zusätzlich verdichten: „Man kann den Raum komplett mit Regalen auffüllen.“ Mindestens 25 Prozent Flächenersparnis seien so möglich, bei vormals manuellen Lagern auch mehr: Der Sanitärgroßhändler SHT konnte dank der Ylog-Shuttles sein Lager von 2000 auf 200 Quadratmeter eindampfen. Die Kommunikation funktioniert nach dem Prinzip einer Taxizentrale: „Die Shuttles bekommen nur die Zielkoordinaten übermittelt und suchen sich den Weg selbst.“ Das hält vor allem bei größeren Flotten den Software- Aufwand für die Steuerung in Grenzen. Fortsetzung auf Seite 2: Wachstumsschmerzen im Lager
Der Automobilzulieferer MSG ist nicht das einzige Unternehmen, in dem höhere Auslastung zu Wachstumsschmerzen im Lager führt. Expandierende Industriebetriebe sind allerorten mit demselben Dilemma konfrontiert: Produktion schlägt Logistik, also müssen Lagerflächen neuen Fertigungshallen weichen. Das Mehr an Vormaterial und Produkten muss auf – zum Teil wesentlich – kleinerer Fläche umgeschlagen werden. Am Anfang steht oft eine Aufräumaktion, an deren Ende Automatisierung schnellere Umschläge ermöglicht: Historisch gewachsene Zwischenlager entlang der Fertigungsstraßen werden durch automatische Kleinteilelager ersetzt, die Arbeitsplätze und Maschinen auftragsbezogen mit den nötigen Teilen versorgen. Aus dem Materialbestand wird endlich ein Materialfluss.Gefragt sind Lösungen aus einem Guss, denn bei gestückelter Intralogistik drohen Reibungsverluste, wie Torsten Tolle vom Prozessberater BPE Solutions beobachtet: „Hoher Wareneingang führt zu Platzmangel, dieser zu mehr Außenlagern, diese zu höherem Transportaufwand, der wiederum koordiniert werden muss. Immer mehr Transaktionen sind zu konsolidieren, immer häufiger kommt es zu Fehlern oder Verspätungen – am Ende sind Speditionen, Kunden und Mitarbeiter gleichermaßen frustriert und die Bottom-Line geht runter.“ Wächst das Unternehmen, hechelt die Logistik immer weiter hinterher. Zumtobel: Fertigung mundgerecht beliefernEine Alternative ist die radikale Neugestaltung einer historisch gewachsenen Lagerlandschaft. Daran macht sich gerade der Leuchtenhersteller Zumtobel, um die geplante langfristige Produktionssteigerung logistisch verkraften zu können. Bis 2013 wird die gesamte Lagerstruktur komplett umgekrempelt: Das Außenlager für Roh- und Halbfertigwaren wird in die Produktion im Stammwerk integriert, ein automatisches Kleinteilelager ersetzt die Puffer in der Fertigung, im bestehenden automatisierten Palettenlager wird die Kommissionierzone erweitert, dafür wird das Fertigwarenlager zu einem Logistikdienstleiter ausgelagert. Notwendig wird die Radikalkur wegen der ehrgeizigen Expansionspläne von Zumtobel-Chef Harald Sommerer: Bis 2020 soll die Produktionsmenge um 70 Prozent steigen. Die Steilvorlage für Thomas Bischof, Werksleiter in Dornbirn: Die Volumensteigerung in der Produktion darf sich nicht 1 zu 1 in einem Logistikflächenzuwachs niederschlagen. „Wir gehen davon aus, dass wir nur rund 20 Prozent mehr Lagerfläche brauchen und den Rest durch Prozessverbesserungen hereinbekommen.“ Das Außenlager im einige Kilometer entfernten Hohenems aufzulösen, wird eine Menge Zeit einsparen: „Heute haben wir in der Produktion ab und an Wartezeiten durch die LKW-Zulieferung.“ Von Hohenems nach Dornbirn verkehren die LKWs zwischen 6 und 22 Uhr im Stundentakt, zu Spitzenzeiten sind es zwei pro Stunde. Wenn ein LKW wegen einer größeren Warenanforderung schon voll ist, kommt eine von der Fertigung angeforderte Teilelieferung erst auf dem nächsten eine Stunde später mit. Die Folge: In der Produktion muss Bischof heute größere Materialmengen vorhalten. Damit ist bald Schluss: Mitte 2012 geht in Dornbirn ein automatisches Kleinteilelager in Betrieb, im Jahr darauf übersiedelt das Material- und Halbfertigwarenlager von Hohenems ins Stammwerk. „Dann können wir die Puffer eliminieren und die Fertigung automatisiert praktisch mundgerecht beliefern.“Platz gespart wird vor allem in der Distributionslogistik: Das gesamte Zumtobel-Fertigwarenlager wird an einen externen Dienstleister ausgelagert. Dabei geht es um die Infrastrukturinvestition, nicht um die Betriebskosten des Lagers, betont Bischof („da sind wir heute auch sehr gut aufgestellt“). Frisches Geld wird lieber für neue Fertigungskapazität als für eine Lagerhalle in Hand genommen. „Außerdem sind wir mit einem Partner skalierbarer“, meint Bischof. Nebenbei schafft Zumtobel sich mit der Auslagerung des Distributionslagers im Stammwerk weitere Flächenreserven für eine künftige Erweiterung – der Produktion natürlich. Fortsetzung auf Seite 3: Henkel CEE - Puffer in die Baulücke
Auch am anderen Ende des Landes steht die Rationalisierung der Lagerlogistik hoch im Kurs. Waschmittelhersteller Henkel CEE eröffnete im Juni ein neues Export- Pufferlager, das direkt an die Produktion in Wien-Erdberg anschließt. Christian Wastl, Logistikleiter von Henkel CEE, beschreibt die Zielsetzung des Neubaus: „Früher hatte das manuelle Lager im Werk mehr als 3000 Quadratmeter. Die Tonnage im Werk wuchs um 30 Prozent, die Lagerfläche wurde aber auf 1400 Quadratmeter reduziert.“ Die Lösung der Stauchung: ein von Siemens konzipiertes mehrstöckiges automatisches Kanallager in einer Baulücke auf dem Werksgelände. Es fasst auf fünf Etagen 1500 Paletten und schaffte so Platz für die sich ausdehnende Produktion. Alle Fertigungslinien transportieren jetzt rund um die Uhr palettierte Ware über automatische Fördersysteme in das Exportlager. Hier werden die Paletten nach Ziel sortiert. Zwei Slipchain-Belader versorgen die Shuttle-LKW, die das zwölf Kilometer entfernte Henkel-Zentrallager Meidling anfahren, von wo aus Kunden in Österreich, Slowenien, der Slowakei und Tschechien beliefert werden. Die Transporte sind schnell getaktet: In drei Minuten ist ein Sattelzug voll. „Vorher hat man sich die Ware händisch auf 3000 Quadratmetern zusammensuchen müssen – jetzt hat sich die reine Verladerampen-Zeit mehr als halbiert“, sagt Wastl. Manuell an drei eigenen Ladetoren beladen werden in Erdberg nur noch die LKW, die direkt an nationale Henkel-Distributionslager in anderen osteuropäischen Ländern gehen. Der automatisierungsbedingt höhere Durchsatz macht die Wiener Lagerlogistik so wettbewerbsfähig, dass ein Distributionslager in Ungarn eingespart werden kann. „Die Kosten sanken signifikant“, freut sich Wastl. Persilflaschen für Györ und Budapest brauchen ab März 2012 von der Abfüllung in Erdberg bis zum Aufladen auf den Kunden-LKW in Meidling keinerlei manuelles Handling mehr: „Derzeit laufen 40 Prozent der Produktion des Werks über das Zentrallager. Wenn wir die Belieferung von Ungarn übernehmen, sind es 60 bis 70 Prozent.“ cargo-partner: Bewusst nicht automatisiertWährend die Produzenten auf ihren Werksgeländen Platz für neue Maschinen und Fertigungsstraßen schaffen, indem sie die Logistikflächen kappen, erweitern die Logistikdienstleister ihre Lager. Zubau bedeutet aber auch bei ihnen nicht notwendigerweise more of the same. Knackpunkt hier ist die Anpassungsfähigkeit der Infrastruktur an die Wünsche verschiedener Kunden. Der Speditionskonzern cargo-partner erweitert gerade sein Verteilzentrum in Fischamend um ein Hochregallager mit 7.000 Palettenstellplätzen, ein Kleinteilelager und eine neue Halle für Cross-Docking im LKW-Sammelgutverkehr. Gewachsen wird mehr in die Höhe als in die Fläche: Die Regale des neuen Lagers sind gut drei Meter höher als die des alten – die neuen Hochregale stellen mit fast 12 Metern Gardemaß auf die maximale Hubhöhe der marktüblichen frei fahrbaren Schubmaststapler ab. Dazwischen geht es lockerer zu: Die Stellplatzhöhe ist frei gestaltbar. Auf eine Automatisierung verzichten die Fischamender Logistiker hingegen wegen der heterogenen Warenstruktur wohlweislich: „Wir haben uns bewusst dagegen entschieden, um höchstmögliche Flexibilität beizubehalten und ein breites Kundenspektrum bedienen zu können“, erläutert cargo-partner-Österreich-Geschäftsführer Christoph Grasl. Effizienzsteigerungen will er lieber beim Energieeinsatz lukrieren: Hochfrequenzladegeräte für die Elektrostapler sollen einige tausend Kilowattstunden pro Jahr einsparen, aus der Reibungswärme beim Bremsen und aus der Absenkleistung des Schubmastes wird Energie zurückgewonnen. Und, klar: Auf das Hallendach kommt natürlich eine Photovoltaikanlage.