Wienerberger Demoplant und AIT : Das neue Wienerberger Demoplant: Nachhaltigkeit ist Hightech Sache
Elektroofen des Wienerbeger-Werks Uttendorf: "Thermodynamische Neuausrichtung des Betriebs"
- © Manfred FeslINDUSTRIEMAGAZIN: Herr Marchner, was war der grundlegende Ansatz hinter dem Bau der neuen, CO₂-neutralen Ziegelfabrik – und warum ging es um mehr als nur den Wechsel des Energieträgers?
Johann Marchner: Uns war von Anfang an klar, dass wir nicht einfach nur Gas durch Strom ersetzen wollten – das wäre zu kurz gedacht. Wir sehen in der Dekarbonisierung der Baustoffproduktion eine zentrale Zukunftsaufgabe und richten unsere Innovationsstrategie zunehmend an den Zielen des European Green Deal aus. Es geht nicht nur um die Reduktion von Emissionen, sondern auch um die Integration kreislaufwirtschaftlicher Prinzipien. Die neue Ziegelfabrik in Uttendorf versteht sich in diesem Kontext als Leuchtturmprojekt für eine klimafreundliche, EU-konforme Industrieproduktion. Ziel war es, den gesamten Produktionsprozess konsequent neu zu denken und technologisch neu aufzusetzen. Dazu gehört etwa der Einsatz automatisierter Transportlösungen wie fahrerlosen Transportsystemen im Werk, aber auch die thermodynamische Neuausrichtung des Ofenbetriebs. Das Projekt hat zwar klaren Demonstrationscharakter, es dient dennoch über unsere Werkstore hinaus als Vorbild.
Welche konkreten Einsparungen konnten im Rahmen des GreenBricks-Projekts erzielt werden?
Marchner: In unserem Werk in Uttendorf konnten wir durch die Umstellung auf elektrisch betriebene Tunnelöfen die CO₂-Bilanz bei der Produktion von Hintermauerziegeln um knapp 90 Prozent verbessern. Gleichzeitig gelang es, den Energieverbrauch um rund 30 % zu senken. Auch beim Trocknungsprozess erzielen wir durch den Einsatz einer Hochtemperatur-Wärmepumpe CO₂-Einsparungen von 80 %. Den Strom für den Betrieb des Brennofens beziehen wir aus der werkseigenen Photovoltaikanlage und decken Restmengen mit zertifiziertem Ökostrom ab. Eine weitere signifikante Einsparung sind die bewusst kurz gehaltenen Transportwege. Unsere Rohstoffe kommen direkt aus der Region. Wir können exakt nachvollziehen, wann und wo er produziert wurde: von der Grube bis zur Baustelle. Dadurch gelingt uns die transparente Ausweisung der Transportemissionen. Ein wichtiger Punkt, denn ein Produkt kann noch so ökologisch erscheinen – wenn es hunderte Kilometer zur Produktionsstätte zurücklegen muss, relativiert sich dieser Vorteil schnell.
Herr Kugi, Sie und Ihr Team waren maßgeblich an der wissenschaftlichen Entwicklung der neuen CO₂-neutralen Ziegelfabrik von Wienerberger in Uttendorf beteiligt. Was waren die wichtigsten technologischen Innovationen, die das AIT beigesteuert hat?
Andreas Kugi: Wir haben auf mehreren Ebenen echte Innovationssprünge erzielt. Die Gesamtenergieeffizienz im Wärmeverbund von Trockner, Brenner und Wärmepumpe konnten wir mithilfe eines digitalen Zwillings gezielt optimieren. Ein weiterer Meilenstein war die Entwicklung und Optimierung von Komponenten des weltweit ersten elektrischen Hochtemperatur-Tunnelofens, der Temperaturen von über 900 Grad Celsius erreicht. Ergänzend dazu entstand eine CO2-neutrale Tonmischung, die exakt auf die neuen thermischen Bedingungen abgestimmt ist.
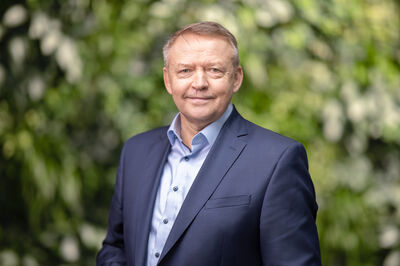
Welche konkreten Effizienzgewinne konnten durch den Einsatz des digitalen Zwillings in der Ziegelproduktion erzielt werden – und inwieweit lässt sich dieser Ansatz auch auf andere Industriezweige übertragen?
Kugi: Der digitale Zwilling bildet das Wärmenetz virtuell ab und verknüpft physikalische Modelle mit Echtzeitdaten der Anlage. Dies ermöglicht einerseits eine gezielte Steuerung und Regelung des Energieeinsatzes im laufenden Betrieb und damit eine Optimierung der Energieeffizienz. Andererseits können veränderte Rahmenbedingungen im Ziegelherstellungsprozess und deren Auswirkungen auf das Zusammenspiel von Trockner, Wärmepumpe und Elektroofen im Voraus simuliert und entsprechend berücksichtigt werden. Der Ansatz lässt sich auf zahlreiche energieintensive Branchen wie etwa die Glas-, Stahl-, Papier- oder Zementindustrie übertragen. Das NEFI-Forschungsprojekt „GreenBricks“ ist grundsätzlich so angelegt, dass die gewonnenen Erkenntnisse auch für andere Sektoren und Branchen verwendbar sind.
Der neu entwickelte elektrische Hochtemperatur-Tunnelofen ersetzt erstmals fossile Brennstoffe in einem energieintensiven Produktionsprozess. Welche technologischen Herausforderungen mussten bei der Umsetzung gemeistert werden?
Kugi: Eine zentrale Herausforderung bestand in der Auslegung der Luftführung im elektrischen Tunnelofen sowie in der optimalen Platzierung der elektrischen Heizelemente. Die Wärmeverteilung im Brennprozess von Ziegeln ist hochkomplex und erfolgt auf mehreren Ebenen: Sie beginnt bei jedem einzelnen Ziegel und setzt sich über die geschichteten Ziegelstapel hinweg fort. Diese Stapel werden auf Wagen platziert, die nacheinander durch den Brenntunnel fahren und dabei verschiedene Heiz- und Kühlzonen mit jeweils unterschiedlichen Betriebsbedingungen durchlaufen. Um die Produktqualität am Ende der Prozesskette sicherzustellen, müssen zahlreiche Parameter präzise aufeinander abgestimmt und optimiert werden. Dazu zählen die Fahrgeschwindigkeit und Verweildauer der Ziegelwagen in den jeweiligen Zonen, die Leistung und geometrische Anordnung der Heizelemente und die gezielte Luftführung in jeder Zone. Angesichts dieser Komplexität sind für eine fundierte Analyse und Optimierung aufwändige dreidimensionale Simulationen notwendig.
Dieser Artikel entstand in Kooperation mit AIT.
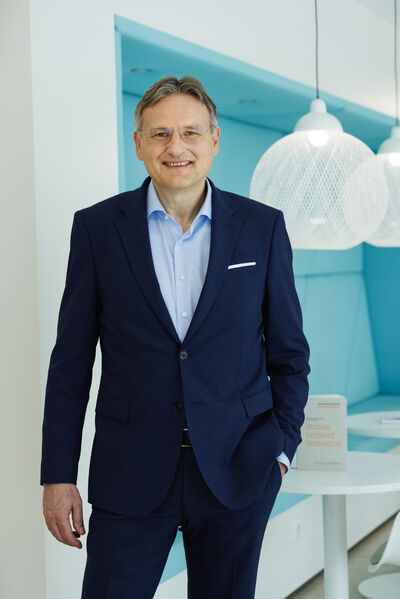