Maschinenbau : Die 5 hartnäckigsten Mythen in der Maschinenentwicklung
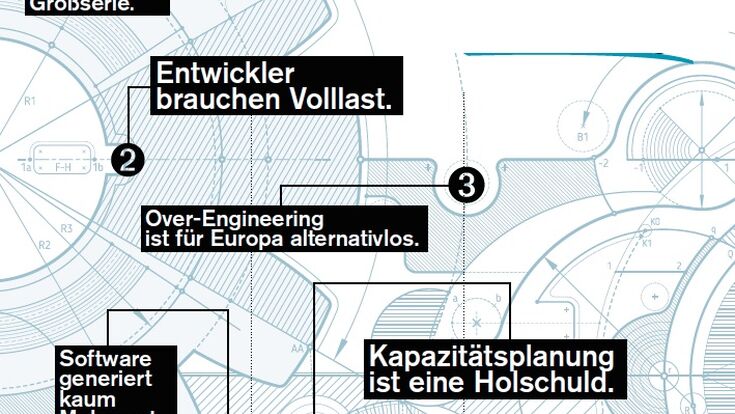
Es ist ein Asset, das den Traunern schon viel Freude bereitet hat: Die konsequente Standardisierung von Kernkomponenten in ihren Transferzentren. Vom Maschinenbett bis zum Werkzeugwechslersystem oder der Hydraulik: Mit großer Akribie hat der oberösterreichische Maschinenbauer Anger Machining ein modulares Maschinenkonzept auf die Beine gestellt, das sich vor allem bei der Entwicklung einer flexiblen Maschine für die Zerspanung von Präzisionsteilen in der Mittel- und Großserie (FLXBL) bezahlt machte: Die Maschine ist jederzeit für neue Bauteile rekonfigurierbar und wird für Kunden zum Multifunktionsträger. Profitieren kann freilich auch der Hersteller selber. Der Einsatz von Gleichteilen ist nicht nur im Einkauf ein spürbarer Hebel. "Wir erreichen in der Montage auch eine signifikante Beschleunigung der Durchlaufzeiten", schildert Anger-Geschäftsführer Klaus Dirnberger. Und es half bei der Suche nach frischem Geld: Der neue Mehrheitseigentümer Tongtai aus Taiwan entlarvte das modulare Maschinenkonzept als Trauner Stärkefeld.
Gleichteileprinzip für alle
Automobilbauer leben es mit großem Tempo vor: Sklavisch folgen sie in der Produktentwicklung dem Gleichteileprinzip, Plattformkonzepten und schrauben am automobilen Baukasten. Dem Fahrzeugkäufer mag es gleichgültig sein: Um die explodierende Variantenvielfalt kostenmäßig abzubilden, müssen Hersteller längst auf eine Modulstrategie für Motoren- und Karosseriebauteile setzen. Und sie haben damit Erfolg: Das aus dem Baukasten produzierte Auto macht Radstand und Spurweiten veränderbar, die Bauteilvarianz sinkt. Auch Maschinen- und Apparatebauer preschen vor – allerdings tun sich einige schwer mit der Umsetzung, wie eine Studie des Maschinenverbands VDMA zuletzt herausfand: Fast die Hälfte aller Forschungs-, Entwicklungs-und Konstruktionsabteilungen der Maschinenbaubranche würden ihre Projektziele verfehlen, heißt es darin mahnend. Lean Entwicklung sieht anders aus. Auch Arko Steinwender vom Geschäftsbereich Produktions- und Logistikmanagement bei Fraunhofer Austria glaubt nicht, dass das Baukasten-Prinzip im Maschinen-, Anlagen- oder Apparatebau, hauptsächlich bei kleineren Unternehmen, schon mit gleichem Erfolg wie in der Automobilindustrie zur Anwendung gebracht werde. Er ortet fehlende Strukturen, Kapazitäten oder Prozesse - aber auch falsche Vorstellungen darüber, wie eine effizientere Maschinenentwicklung, beispielsweise durch gezielten Methodeneinsatz aus dem Technologie- und Innovationsmanagement, aussehen kann.
Allzu viele Details darf Leopold Mader über die nagelneue Versiegelungsmaschine noch nicht preisgeben. Schließlich wird die Produktion der Maschine erst Ende des Jahres anlaufen. Zuviel verrät der Leiter Innovation & Forschung beim niederösterreichischen Glasbearbeitungsmaschinenbauer Lisec allerdings nicht, wenn er auf den sich jetzt schon abzeichnenden Entwicklungserfolg zu sprechen kommt: Die Prozesse der Maschine wurden nicht nur auf noch höhere Leistung getrimmt, sondern auch auf Teilereduktion ausgelegt: Ein Drittel weniger Bauteile sind nun dank einer größeren Umkonstruktion der Maschine bei gleichzeitig höherer Standardisierung verbaut – das betrifft unter anderem verstellbare Transporteinheiten oder Antriebe, die nun nicht mehr nötig sind. Der Hersteller fertigt das Modell in Klein- und Mittelserie und nicht in Riesenlosen – die Maschine von Grund auf stärker als Baukasten zu denken, rentiert sich für Lisec nicht weniger. Vor allem auch deshalb, weil
die Niederösterreicher verschiedene Technologien wie das Glashandling konsequent über mehrere Maschinentypen denken. "Das ziehen wir auch durch", sagt Mader.
Kaum ein Betrieb nimmt bei der Steuerung seiner Konstruktionsteams die Durchlaufzeiten in den Fokus. Zu dem Schluss kommt die VDMA-Studie "Lean-Development im Deutschen Maschinenbau", die das Beratungshaus Staufen durchführte. Stattdessen steht die reine Auslastung der Mitarbeiter im Vordergrund. Besonders alarmierend: Mehr als 73 Prozent der Befragten überplanen die Auslastung der Mitarbeiter und Ressourcen zu mehr als 80 Prozent. "So verbleiben weder Puffer für Feuerwehraktionen noch Flexibilitätsreserven für prozessverbessernde Maßnahmen", heißt es in der Studie. Was dazukommt: Damit verstoßen die Hersteller gegen ein zentrales Prinzip von Lean Management, rügen die Studienautoren. "Denn nur die Priorisierung nach der Durchlaufzeit deckt Störungen im Entwicklungspozess auf", heißt es in der Untersuchung. Konkrete Handlungsempfehlung der Deutschen: Führen Sie Methoden des Shopfloor-Managements in Ihrer Entwicklungsabteilung ein! Eine Visualisierung der Projektziele kann der erste Schritt sein. Und so ganz glauben Entwickler ohnehin nicht, schon sonderlich lean zu entwickeln: Gerade einmal jeder zweite erachtet die Regelkommunikation in seiner Abteilung als standardisiert, zeiteffizient und – problemlösungsorientiert.
Es ist ein Betrachtungswinkel, dem Premiumhersteller geneigt bleiben: Maschinen für die europäischen Hightech-Märkte müssten vollbepackt mit Spitzentechnologie sein. Laissez-faire könne man sich vielleicht anderswo leisten, aber nicht hier. Natürlich wird das keiner grundsätzlich in Abrede stellen. Ein deutliches Missverhältnis dabei, was eine in Deutschland oder Österreich abgesetzte Maschine können sollte und tatsächlich kann, besteht in vielen Fällen dennoch. Und so ist im Engineering nicht nur eine gesunde Mischung aus Struktur und Kreativität eine Anforderung, wie es bei einem heimischen Maschinenbauer heißt. Hersteller müssen auch über neue Organisationsformen nachdenken. Der Trauner Maschinenbauer Anger hat sich bereits ein Toolset erarbeitet, das dem Over-Engineering entgegenwirkt: Das strukturierte Phasenmodell, das die Oberösterreicher zur Anwendung bringen, erfasst und priorisiert Marktbedürfnisse, die letztlich dort aufgegriffen werden, wo es einzig Sinn macht: in der Maschinenentwicklung. Die periodische Rückkopplung mit Vertrieb und Fachexperten nehmen die Trauner somit ernst, die Arbeit im Engineering endet nicht nach der Auslieferung der Maschine. "Das Feedback des Kunden
im laufenden Betrieb dient dazu, unsere Maschine konstruktiv – und auch kostenseitig – weiter zu optimieren", so Anger-CEO Klaus Dirnberger.
Man wünschte sich, es wäre anders, aber: Das Bild mit Arbeit zugeschaufelter Entwicklungsabteilungen ist vielfach ein realistisches. Für Frank Bünting, stellvertretender Abteilungsleiter Betriebswirtschaft beim VDMA, wäre es deshalb jetzt an der Zeit, an einigen Schrauben in der Produkt- und Technologieentwicklung zu drehen. Vor allem an der hohen Zahl der Entwicklungsaufträge, die gleichzeitig in die F&E-Abteilungen gepresst würden, stößt er sich: "Vergleichen Sie es mit der Fertigung: Wo Kapazitäten für zehn Aufträge da sind, schiebt man zwölf oder 15 rein“. Das Ergebnis: "Sie blockieren sich gegenseitig", sagt Bünting. Soweit lassen es manche Maschinenbauer nicht kommen. "Wir haben klar geschützte Ressourcen, um nicht Gefahr zu laufen, die Entwicklungsarbeit zu bremsen, wenn ein wichtiger Kundenauftrag hereinkommt", heißt es beim Maschinenbauer Anger. Darüber hinaus schnüren die Oberösterreicher kleinere inhaltliche Arbeitspakete. Interdisziplinäre Teams bearbeiten diese mit kurzen Monitoring-Zeiten – sogenannten wöchentlichen "Sprints".
Technologieverständnis und Kreativität – beides ist für Entwickler unbezahlbar. Anderseits: Alles andere als ein Durchdringen der Konstruktionsabteilungen mit intelligenter Software wäre eine Überraschung: Innovative IT-Tools bahnen sich ihren Weg und tragen immer deutlicher zum entwicklerischen Erfolg bei. So arbeiten Hersteller schon länger mit Produktdatenmanagement-Tools, die selbstverständlich die richtigen Schnittstellen zu Konstruktionstools besitzen. Aber auch immer ausgefeiltere Algorithmik kommt aus der digitalen Welt: So sorgt ein Tool für die automatische Parametrisierung von Stiegenaufgängen rund um Produktionsanlagen für deutlich schnellere Konstruktionszyklen.