Die Strategien der Sieger : Wettbewerb Fabrik2011: Lorbeer und starke Auftritte
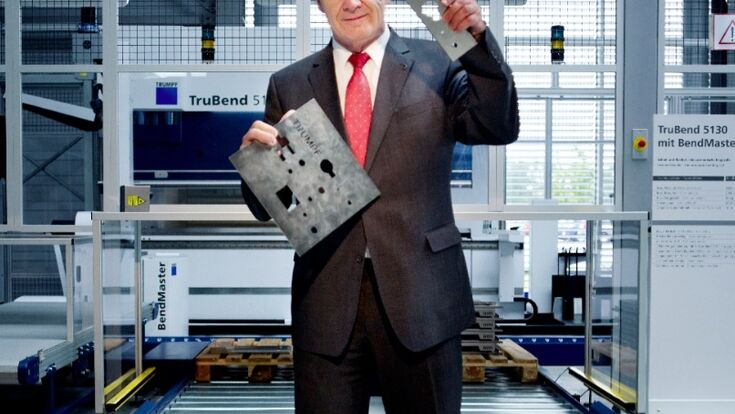
Am Ende flatterten die Nerven. 350 Personentage investierten die Fraunhofer-Experten für die Evaluierung der elf Vorfinalisten von Fabrik2011 – wer es ganz hinauf aufs Treppchen schaffte, entschied sich aber erst am Industriekongress in Linz. Vier Betriebe – zwei in der Kategorie „Unternehmen“ (unter 5000 Mitarbeiter) und zwei in der Kategorie „Konzerne“ – zogen ins Finale ein. Den Gesamtsieg holte nach packendem Finish der Paschinger Maschinenbauer Trumpf Maschinen Austria. Er ging in der Kategorie „Konzerne“ vor dem Motorenwerk Opel Wien durchs Ziel. Bei den „Unternehmen“ siegte mit tadelloser Performance der Analogchiphersteller austriamicrosystems, der Produktionsdienstleister APF schaffte es auf Rang Zwei. Die vier Topbetriebe sind gekürt, doch was zeichnet sie aus? Alle Fotos von der Preisverleihung "Fabrik 2011" finden Sie hier. Seite 2: Gesamtsieger Fabrik2011 & erster Platz Kategorie „Konzerne“: Trumpf Maschinen Austria - Innovationslok in Fahrt
Dem Konzernecho schenken die Paschinger immer ein Ohr. Genau hingehört hat Alfred Hutterer, Chef von Trumpf Maschinen Austria, deshalb auch, als die deutsche Konzernmutter kürzlich zur jährlichen Zeugnisvergabe schritt. Für die Produktion der Oberösterreicher gab es – nicht zum ersten Mal – „Bestnoten“, registrierte Hutterer zufrieden. Reinen Wein schenkte dem Maschinenbauer auch die Fabrik2011-Jury ein. Einen ziemlich bekömmlichen sogar. „Der Betrieb fährt seit Jahrzehnten eine unheimlich konsistente Strategie“, befand Jurymitglied Knut Consemüller, der mit Erich Becker, Claus Raidl und Florian Zangerl die Viererjury stellte. Es gebe „eine unglaubliche Kontinuität im Management“, sagte er auch. Und: Die Standortstrategie des Unternehmens sei „top“, lobte Jurymitglied Becker. Fließfertigung auf höchstem Niveau. Sparsamkeit, Fleiß und unternehmerisches Geschick: Die schwäbischen Tugenden wirken auf den Paschinger Standort durch. Schon 1999 preschte der Betrieb mit einer Fließlinie für die Montage von Biegemaschinen vor. Auch heute ist Trumpf – zumindest im Maschinenbau – mit den modernen Fließlinien für Abkantpressen und Roboter immer noch ein Exot. Zwölf unterschiedliche Typen des Hydrauliksegments, über tausend Maschinen pro Jahr, fertigen die Oberösterreicher auf einer Linie. So effizient, dass „wir in der Krise bei halbiertem Umsatz immer noch Gewinne schrieben“, sagt Betriebsleiter Thomas Saiko. Zuletzt holte der Betrieb sogar die Fertigung von Einstiegsmaschinen nach Pasching. Früher in Taiwan produziert, geschieht dies nun „weit effizienter in unserem Werk“, lacht Saiko. Was den Oberösterreichern dabei in die Hände spielt? Laut Jury das Produktionssystem (Synchro). An dem fand sie nur gutes. „Wir ziehen damit die Aufträge durch die Fertigung“, erklärt Technikchef Armin Rau. Das Montageband läuft im Kundentakt. Keine Sekunde zu früh oder zu spät sind die Teile beim Monteur. Dafür sorgen auch fünf Kommissionierer. Selbst in der Werkzeugproduktion kommen die Paschinger ohne Zwischenpuffer aus. Für Fertigungsbetriebe ein mitentscheidender Grund, hier einzukaufen: „In 17 Tagen bauen wir jede Maschine, die der Kunde haben will“, so Rau. Innovationstreiber. Der Betrieb sei „in seinem Bereich sehr innovativ“, urteilte Juror Florian Zangerl. Den Fortschritt habe man sich „ins Stammbuch geschrieben“, bestätigt Alfred Hutterer. Dass es dafür Preise gibt, sei „umso schöner“. So schnitt der Betrieb schon vor zwei Jahren beim Oberösterreichischen Innovationspreis gut ab. „Die „schnellste Biegemaschine“ wurde mit dem dritten Platz geadelt. In der Krise gelauncht, „bauen wir davon heute 300 Stück pro Jahr“, so Hutterer. Auch die Optimierungen, die die Paschinger in ihrem Werk anstoßen, sprach die Jury an. Der aktuelle Zustand der Fertigung sei immer „der denkbar schlechteste“, weiß Hutterer, wie er sein Team zu neuen Großtaten motiviert. In Maschinenlerninseln und Planspielen wird Weiterbildung „auf hohem Niveau“ praktiziert, so die Jury. Kurzschulungen oder Dreitagesworkshops – „wir ziehen alle Register“, bestätigt Technikchef Armin Rau. Die Jury sah es genauso – ein klarer Gesamtsieg. Seite 3: Erster Platz „Unternehmen“: austriamicrosystems AG - Muskelspiele in der Scheibenwelt
Werksbesichtigungen gehören in Unterpremstätten zum „weekly business“. „Wir haben laufend internationale Besucher hier“, erzählt Walter Mente, Betriebsleiter von austriamicrosystems. Als solcher führte er in der heißen Evaluierungsphase von Fabrik2011 auch die Fraunhofer-Experten durchs Werk. „Klassenbester“ in der Produktion analoger Mikrochips wolle man sein. Deshalb rechneten sich die Steirer auch Chancen bei Fabrik2011 aus. Mit der Einschätzung lagen sie nicht schlecht. Ob Chips für Flachbildfernseher oder Halbleiter für die Medizintechnik und Autoindustrie: Das Werk tritt gegen internationale Riesen an – “und macht alles richtig“, urteilte Fabrik-2011-Juror Knut Consemüller. Scheibenfertigung auf Topniveau. Das Herz des Halbleiterspezialisten (Umatz 2010: 209 Millionen Euro) ist ganz klar die Scheibenfertigung. Auf 120 Maschinen (Gesamtwert: 350 Millionen Dollar) stellt der Betrieb pro Jahr 110.000 Siliziumscheiben für mehrere Millionen Halbleiter her – „seit 2001 vollautomatisiert“, erzählt Betriebsleiter Walter Mente. Beeindruckende Halbleitermaschinen und Diffusionsöfen reihen sich an Lithographiemaschinen, die feinste Strukturen belichten können. 100 Maschinenbediener arbeiten in der Scheibenfertigung. Dazu kommen noch einmal so viele Ingenieure und Wartungsprofis. Eine hochkarätige Truppe, „58 Prozent haben einen akademischen Abschluss“, betont Mente. Stillstände oder Schlechtteile? Sind äußerst selten. Denn seit 2009 ist die vorbeugende Instandhaltung bei austriamicrosystems Geschichte. Der Betrieb sattelte auf eine vorausschauende Wartung um. „Wartungszeit ist tote Zeit“, weiß Mente. Mit einer Software zur statistischen Prozesskontrolle (SPC) schaut der Betrieb deshalb nicht nur aufs Produkt. Auch die Maschinenparameter behält er im Auge. „Ein Leck am Implanter finden wir genauso schnell wie einen kaputten Dichtring“, meint der Betriebsverantwortliche. Ausgeprägtes Kennzahlensystem. Ein selbstbewusster Ansatz, der bei der Wettbewerbsjury extrem gut ankam. Jury-Lob gab es aber auch für das Kennzahlensystem. Schlüsselwerte werden „wie im Flugzeugcockpit dargestellt“, vermerkte die Jury positiv. „In drei Sekunden sage ich jedem, was wo läuft und steht“, versichert Mente. Nicht überraschend: Der Anspruch, „Klassenbester“ zu sein, führte den Betrieb vor drei Jahren in die USA. „Wir starteten dort eine Entwicklungskooperation mit dem IBM-Konzern, selber Betreiber einer Scheibenfertigung“, sagt Mente. Heute ernten beide die Früchte ihrer Arbeit. Mente: “Wir produzieren nahezu verschwendungsfrei”. Sonderpreis Energieeffizienz: austriamicrosystems - ein Stück Regenwald für Afrika Das Energiekonzept der Unterpremstättener hat uns „voll überzeugt“. Mit der Begründung erklärte die Fabrik2011-Jury den Chiphersteller austriamicrosystems zum Sieger des heurigen Energieffizienz-Sonderpreises. Natürlich wurde eine Detailbetrachtung angestellt: Der Betrieb nutze seit dem heurigen Jahr hundertprozentig „grünen“ Strom, ziehe ein Biomassekraftwerk hoch (Hackschnitzel!) und plane die Pflanzung eines Regenwaldstücks in Uganda, um spätestens 2015 „CO2-neutral zu bilanzieren“, fasste die Jury in ihrer Siegerbegründung staunend zusammen. Weiters hat gefallen: Die Haustechnikabteilung der Steirer, die größer als manch ein Produktionsbetrieb ist (42 Mitarbeiter). Sie hält die technische Infrastruktur am Laufen. Und sucht „nach weiteren Einsparpotentialen“, schildert austriamicrosystems-Energiexperte Karl Müller. So lautete unlängst eine Fragestellung, wo denn nun des Sommers der „optimale Betriebspunkt“ der Lüftung liege. Und wie mit weniger Energieaufwand das entsalzte Wasser zum Reinigen der Chips bereitgestellt werden kann. “Ziemlich beeindruckend“, fand Fabrik2011-Juror Claus Raidl. Seite 4: Zweiter Platz "Konzerne": Opel Wien - Rotation in Perfektion.
Mit den Pfunden wuchern wollten beide nicht. Nicht das BMW Motorenwerk in Steyr, lorbeerüberhäufter Vorjahressieger des Fraunhofer-Industriewettbewerbs. Und auch nicht Opel Wien, Vorfinalist des Jahres 2010. Also spulten die beiden Fabriken bald nach dem Wettbewerb Betriebsbesuche ab. Die Steyrer schauten sich einiges von den Wienern ab. Und das Getriebe- und Motorenwerk Wien-Aspern nahm „wertvolle Impulse“ aus Oberösterreich mit, wie es Opel Wien-Generaldirektor Rudolf Hamp astrein trifft. So hinterließ die auftragsbezogene BMW-Fertigung einen großen Eindruck. „Wir haben dazu selber ein Projekt angestoßen“, bestätigt Opel Wien-Technikchef Isfried Janetschek. Die Ernsthaftigkeit, mit der das geschah, entging auch der Fabrik2011-Jury nicht. Bestnoten aber setzte es nicht nur dafür. „Das Motorenwerk ist in mehrerlei Hinsicht spitze“, so Fabrik2011-Experte Daniel Palm. Mitarbeiterrotation hält die Montage flexibel. Schon heute fertigen die Asperner im Motorensegment 67 verschiedene Typen. Denn Flexibilität – das zeigten die Krisenmonate – sei angesichts von Volumenschwankungen „ein Überlebensprinzip“, so Hamp. Das schnelle „Umschichten“ von Mitarbeitern auf andere Montageplätze hob die Wettbewerbsjury deshalb hervor. Dies praktiziere Opel „vorbildhaft“, so das Fazit. Ist in der Motorenmontage Not am Mann, springen Mitarbeiter aus der Sechsgang-Getriebemontage ein. Und es gibt ein Rotationsprinzip – das ein Einrosten verhindert. Alle Monteure wechseln „turnusmäßig in andere Arbeitsbereiche“, so Janetschek. Teamsprecher würden die gesamte Motorenmontage beherrschen – immerhin „30 Stationen“, sagt er. “Autonome“ Instandhaltung. Der kontinuierliche Verbesserungsprozess (KVP) ist im Motorenwerk heute ebenfalls gut eingeführt. Neben verbaler Anerkennung gibt es auch bei Opel geldwerte Motivation, seinen eigenen Arbeitsplatz „nicht härter, sondern smarter zu machen“, sagt Generaldirektor Rudolf Hamp. So strichen die Mitarbeiter in der Zahnradfertigung in einer kreativen Stunde einen gesamten Schruppprozess. Mehrfach optimiert sind auch die Arbeitsplätze: Ähnlich „dem Lesebereich einer Supermarktkasse“ versuchen die Asperner, alles „in Griffnähe zu haben“, erklärt Hamp. Gelebt wird auch das Thema Instandhaltung. 400 Instandhalter sorgen dafür, dass 1500 Einzelanlagen wie geschmiert laufen. In einem EDV-System sind alle Wartungspläne und die Maschinenhistorien hinterlegt. Nicht immer rücken im Opel-Werk aber gleich die Instandhalter aus. Die „autonome“ Instandhaltung entlastet die Fachkräfte. Jeder Monteur prüfe selber „Keilriemen oder das Ölniveau“, so Janetschek. Seite 5: Zweiter Platz "Unternehmen": APF Produktionsdienstleistungs GmbH - Vollautomation als Festakt
Im Vorjahr juckte es Hermann Landershammer schon im kleinen Finger. Eingehend studierte er den Fraunhofer-Fragebogen – doch letztlich, erzählt der Chef des Gamperner Stiwa-Produktionsdienstleistungsbetriebs lachend, habe „ihm der Mut gefehlt, mitzumachen“. Davon kann heute keine Rede mehr sein. Beherzt entschieden sich die Oberösterreicher heuer für die Wettbewerbsteilnahme – ihr Mut wurde prompt belohnt. Gleich auf Anhieb schaffte es der Baugruppenfertiger ins Fabrik2011-Finale. „Weniger der unbedingte Siegeswille überwog“, sagt Landershammer, „es war mehr die Neugierde“. Der Betrieb wollte nicht mehr länger nur im eigenen Saft braten. Wo grenzt man sich von anderen ab? „Das wollten wir unbedingt herausfinden“, so Landershammer. Schwindelerrregende Prozessüberwachung. Die Stiwa Automation stellt Automatisierungssysteme her. Die Konzernschwester APF entwickelt und fertigt auf solchen Anlagen seit 2003 Systembaugruppen, etwa Führungskästen für ThyssenKrupp oder Beschläge für Blum. Auch bei Volkswagen hat der Betrieb wichtige Nominierungen geschafft. Laserschweißen, Spritzgießen, Stanzen, Zerspanen und Montieren sind die Standbeine der Oberösterreicher. Der größte Umsatzbringer sind die Führungskästen für Lenksäulen – sie machen mehr als zwei Drittel des Geschäfts aus. Acht Millionen Stück produziert die APF davon jährlich. Wie, das beeindruckte die Fraunhofer-Jury schwer. Die Gamperner, so das einhellige Fazit, haben den Bogen heraus, wie mit Software – etwa einem Qualitätssicherungstool – die Fertigung überwacht werden kann. Lückenlos. „Die Softwareintegration ist der Schlüssel”, bestätigt APF-Chef Landershammer. Fahrerlose Transportsysteme schleusen Bleche vom Hochregallager direkt an die Bearbeitungsmaschinen. Schon im Lager werden Qualitäts- und Lieferdaten aufgezeichnet – „das erhöht die Rückverfolgbarkeit“, sagt Landershammer. Vollautomatisch läuft auch die Fertigung selber ab. Ist- und Solldaten – etwa beim Blechstanzen – vergleicht das System laufend. Fehlteile reduziert der Betrieb so auf ein Minimum. In der Stiwa-Gruppe sei der Betrieb „ein Testfeld“ für Neuentwicklungen. “Das hält uns sehr wettbewerbsfähig”, erzählt der APF-Chef. Taktzeit-Rennen. Als sehr positiv bewertete die Wettbewerbsjury die Taktzeiten bei den drei Laserschweißanlagen. „Auch diese Maschinen sind online-überwacht“, sagt APF-Chef Landershammer. So prüft das System Schweißnähte nach. „Extrem starke Regelkreise“ sind ein Highlight in der APF“, sagte die Jury weiter. So stellt die Maschine dem Technikbetreuer zu Schichtende die fünf häufigsten – und längsten – Störungen in elektronischer Form bereit. Was man zur Topplatzierung sage? Sie sei ein Motivationsschub „für die ganze Mannschaft“, so der AFP-Chef. Daniel Pohselt Alle Fotos von der Preisverleihung "Fabrik2011" finden Sie hier.