Geberit Werk Pottenbrunn holt Award : Geberit Werk Pottenbrunn: So gewann der Kunststofffertiger die Fabrik2024
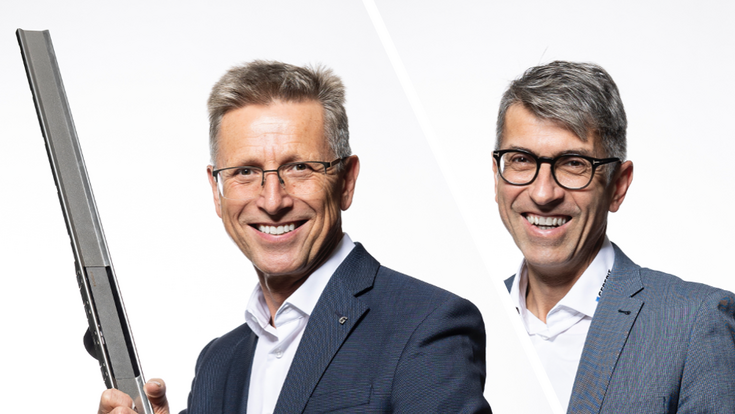
Helmut Schwarzl, Geschäftsführer Geberit-Werk Pottenbrunn und Andreas Fink, Technischer Leiter Geberit
- © Matthias HeschlWoche der Robotik
Liebe Leser*innen,
heute haben wir etwas ganz Besonderes für Sie: Die "Woche der Industrierobotik" vom 2. bis 5. Dezember 2024, komplett online auf allen Portalen!
Steigender Kostendruck, Fachkräftemangel und der Bedarf an Flexibilität in der Produktion & Logistik erfordern innovative Lösungen. Multimedial geben wir spannende Einblicke und die wichtigsten Erkenntnisse rund um den Einsatz von Robotern: Von innovativen Automatisierungslösungen bis hin zu zukunftsweisenden Technologien beleuchten wir eine Woche lang die aktuellen Entwicklungen, Trends und Potenziale.
Wir wünschen Ihnen viel Freude mit unserem außergewöhnlichen Special!
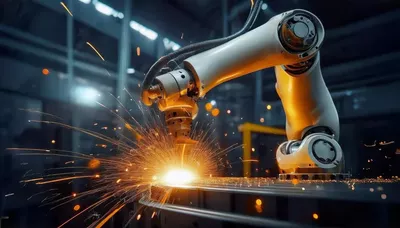
„Wer aufhört, besser zu werden, hört auf, gut zu sein“ – dieser Leitsatz steht für den kontinuierlichen Verbesserungsprozess im Werk Pottenbrunn des Sanitärtechnikkonzerns Geberit. Seit der Eröffnung des Werks 1971 hat sich der Standort kontinuierlich weiterentwickelt und ist heute ein Vorzeigebetrieb, der sowohl auf Lean Management als auch auf Digitalisierung setzt. Das Werk beschäftigt 400 Mitarbeiter, produziert etwa 1.800 verschiedene Produkte und hat sich als Spezialist für Spritzgussverfahren etabliert.
Lesen Sie auch: Fabrik2024: Geberit holt Titel Fabrik des Jahres
In den vergangenen Jahren hat das Werk einen tiefgreifenden Wandel durchlaufen – mit einer klaren Roadmap, die das Ziel verfolgt, eine „ziehende, digitale und standardisierte Fabrik“ zu werden, wie Andreas Fink, Technischer Leiter Geberit am Finaltag des von Fraunhofer Austria und INDUSTRIEMAGAZIN ausgerichteten Produktionswettbewerbs Fabrik2024 in St. Valentin sagt.
RANG 1 + KATEGORIESIEG EFFICIENT FACTORY
Geberit Produktions GmbH & Co KG, Pottenbrunn: Die Leanen
Die Einführung von Lean Management 2007 war ein erster Schritt, um die Effizienz zu steigern und die Prozesse zu optimieren. Mit der Werksstrategie 2016 wurde bei Geberit in Pottenbrunn entschieden, dass eine grundlegende strategische Neuausrichtung notwendig ist. „Kein Stein blieb auf dem anderen“, erinnert sich Helmut Schwarzl, der Geschäftsführer des Werks. Die Produktion wurde komplett neu ausgerichtet, Prozesse neu definiert und die gesamte Organisation auf Zukunftskurs gebracht. „In Wahrheit haben wir die Produktion und das Prozesslayout komplett umgestellt“, sagt Schwarzl. Der Fokus liegt auf der Optimierung von Hauptprodukten wie dem Rohrleitungssystem „Silent-PP“ oder dem Dachentwässerungssystem „Pluvia“. Diese Produkte werden im Wertstrom abgebildet – von der Rohfertigung bis zum Endprodukt. Die Vermeidung von Verschwendung steht dabei im Mittelpunkt. „Es ist ganz einfach: Wir schaffen Werte durch erstklassige Prozesse und sichern dadurch langfristig Arbeitsplätze“, betont Schwarzl. Diese Fokussierung auf Effizienz und Prozessoptimierung sei der Schlüssel zum Erfolg.
Ein weiteres Ziel des Transformationsprozesses war es, eine Produktion zu ermöglichen, die auf einem Pullsystem basiert. „Am Ende wollen wir im Kundentakt fertigen“, so Schwarzl. Das Pullsystem soll sicherstellen, dass nur produziert wird, was tatsächlich nachgefragt wird, um Überproduktion und Lagerbestände zu minimieren. Dieses Prinzip steht in engem Zusammenhang mit der Reduzierung von Verschwendung und der Maximierung der Wertschöpfung.
Führungskultur
Ein zentrales Element des Transformationsprozesses war die Neuausrichtung der Führungskultur. „Nach mehreren Jahren der Anwendung diverser Lean-Tools haben wir festgestellt, dass wir einen größeren Schritt machen müssen“, erklärt Schwarzl. Es wurde ein umfassender Veränderungsprozess eingeleitet, der bis in die Führungsstrukturen hineinreichte. Ein Motto dabei war „Führen vor Ort“: Meister wurden zurück in die Fertigung geholt, um näher am Produktionsgeschehen zu sein und die direkte Verantwortung für die Abläufe zu übernehmen.
Schwarzl und Fink heben besonders das Shopfloormanagement hervor, das durch den sogenannten „9er-Kreis“ und den PDCA-Prozess (Plan-Do-Check-Act) gestärkt wurde. Dieser Prozess sieht vor, dass der Führungskreis täglich für rund 20 Minuten zusammenkommen, um gemeinsam über die Produktion der vergangenen 24 Stunden und den aktuellen Tag zu sprechen, die Zielerfüllung zu überprüfen, Verbesserungsmöglichkeiten zu identifizieren und Probleme unmittelbar zu lösenoder zu adressieren. „Das ist ein unglaublich starkes Instrument“, erklärt Schwarzl, „und es trägt nachhaltig zur Optimierung der Produktionsabläufe bei.“ Die darauffolgenden regelmäßigen Gemba-Walks, bei denen Führungskräfte und Mitarbeiter gemeinsam den Shopfloor begehen, um Abweichungen und Potenziale zu erkennen, runden das Konzept ab.
Prozessoptimierung
Die Umstellung der Produktion bedeutete auch eine Neuanordnung der Maschinen im Werk. Andreas Fink erklärt: „Wir haben sprichwörtlich keinen Stein auf dem anderen gelassen, also keine Maschine auf ihrem alten Platz belassen.“ Stattdessen wurden Maschinen, die für Produkte mit hohem Volumen zuständig sind, nahe am Outbound-Bereich platziert, um den Materialfluss zu optimieren. Besonders kennzahlgetrieben war die Neuanordnung der Hauptprodukte, die nun von derGrundfertigung bis zum Fertigprodukt prozessorientiert und nicht mehr technologieorientiert hergestellt werden.
Für die Hauptprodukte konnten signifikante Effizienzgewinne erzielt werden. Die Logistikflächen wurden durch die Umstrukturierung deutlich reduziert und die Durchlaufzeit für ein Hauptprodukt liegt beispielsweise nach ehemals 19 nun bei fünf Tagen. Fink erklärt, dass dieses Produkt in über 100 verschiedenen Varianten produziert wird und ein hoher Lieferservicegrad besonders im Fokus steht.
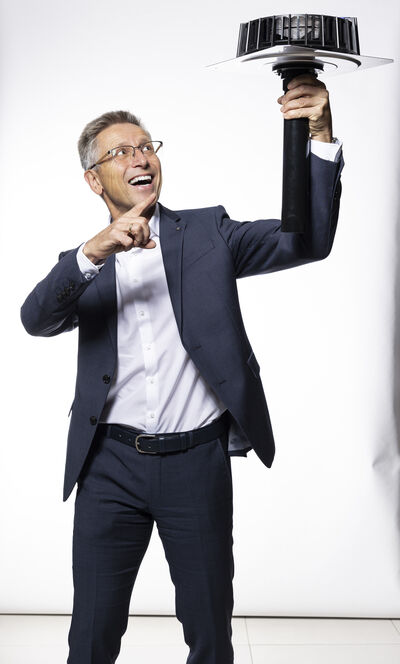
WEBINAR: Lagerrobotik als Gamechanger!
Hawesko zeigt in diesem Webinar, wie AMR-Lagerrobotik den Warendurchsatz steigert und den Personaleinsatz optimiert. Erhalten Sie praxisnahe Einblicke in die Einführung und Systemintegration automatisierter mobiler Roboter. Kostenlos anmelden und Logistik effizienter gestalten!
Wann: Do., 05.12.2024, 10:00 bis 11:00 Uhr
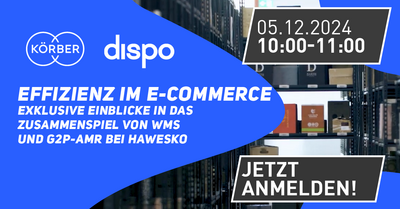
Smartlösungen
Eine zentrale Rolle bei der Optimierung der Produktion spielt die Digitalisierung. Geberit hat in Pottenbrunn auf fahrerlose Transportsysteme (FTS) gesetzt, die den Materialfluss im Werk autonom steuern. „Diese Geräte kommunizieren untereinander über WLAN und optimieren sich selbst“, erklärt Schwarzl. Statt herkömmlicher Gabelstapler werden nun täglich rund 200 Transporte von FTS durchgeführt, was nicht nur die Effizienz steigert, sondern auch die Sicherheit in der Produktion erhöht.
Auch im Bereich der Automatisierung hat sich das Werk Pottenbrunn deutlich weiterentwickelt. Während früher Roboter nur eine untergeordnete Rolle spielten, sind heute 35 Roboter im Einsatz, die in den diversen Montagezellen unterstützen. „Roboter waren früher eine Randerscheinung, heute sind sie fester Bestandteil unserer Fertigung“, betont Schwarzl. Im Bereich der Qualitätsüberprüfung wird mittlerweile auch die KI eingesetzt.
Energieeffizienz
Neben der Effizienzsteigerung hat sich Geberit auch dem Thema Nachhaltigkeit verschrieben. Seit vielen Jahren nutzt das Werk in Pottenbrunn die Abwärme der Produktion, um die Gebäude zu beheizen. Der Einsatz von Gas als Energiequelle wurde auf ein Minimum reduziert. „Die Hochpreisphase bei Strom haben wir durch weitsichtigen Einkauf gut überstanden“, berichtet Schwarzl.
Ein besonderes Augenmerk liegt auf der Reduzierung des Energieverbrauchs. Geberit hat sich das Ziel gesetzt, bis 2035 den CO₂-Ausstoß gegenüber 2015 um 80 Prozent zu senken. Dazu tragen auch die jährlichen Maßnahmen zur Stromreduktion bei, die von einem speziellen Energieteam überwacht werden. „Jedes Jahr streben wir eine Reduzierung des CO₂-Ausstoßesvon fünf Prozent an“, erklärt Schwarzl. Diese Maßnahmen tragen nicht nur zur ökologischen Nachhaltigkeit bei, sondern helfen auch, die Betriebskosten langfristig zu senken.
Förderung von Frauen
Ein weiteres Erfolgsrezept des Standorts Pottenbrunn ist die hohe Flexibilität der Belegschaft. Geberit setzt ausschließlich auf fest angestellte Mitarbeiter – Leiharbeiter werden in der Regel nicht beschäftigt. Die Mitarbeiter wechseln regelmäßig zwischen den Produktionslinien, um tägliche Auftragsschwankungen auszugleichen und die Kapazitäten optimal zu nutzen. „Diese Flexibilität ist ein wichtiger Erfolgsfaktor, um die täglichen Herausforderungen zu bewältigen“, so Schwarzl.
Auch die Förderung von Frauen spielt eine zentrale Rolle in der Unternehmensstrategie. Der Frauenanteil am Standort liegt bei 43 Prozent. Durch gezielte Maßnahmen zur Förderung will Geberit den Frauenanteil in den kommenden Jahren weiter steigern und so die Diversität im Unternehmen erhöhen.
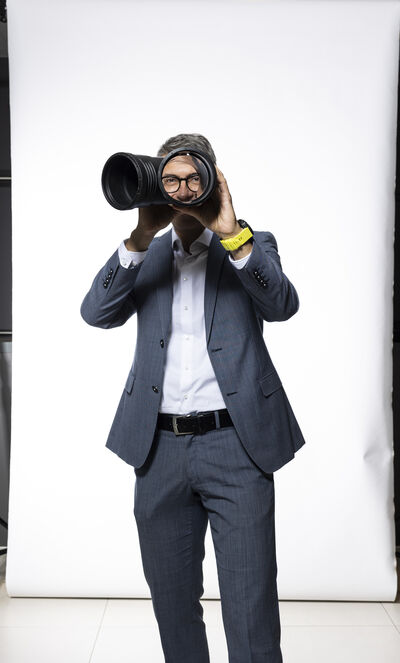
WEBINAR: Kollaborative Robotik für mehr Effizienz – am Beispiel der Blech- und Metallfertigung
Kosten senken, Produktivität steigern: Erfahren Sie im Webinar, wie kollaborierende Roboter (Cobots) die Metallverarbeitung voranbringt. Praxisbeispiele zeigen, wie Prozesse optimiert und flexibel an Anforderungen angepasst werden können. Jetzt kostenlos anmelden!
Wann: Di., 03.12.2024, 14:00 bis 15:00 Uhr
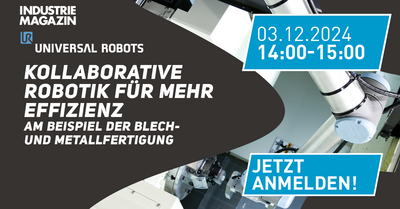