Aluminium und Stahl : Wie Gießereien die Abkehr von Erdgas gelingen kann
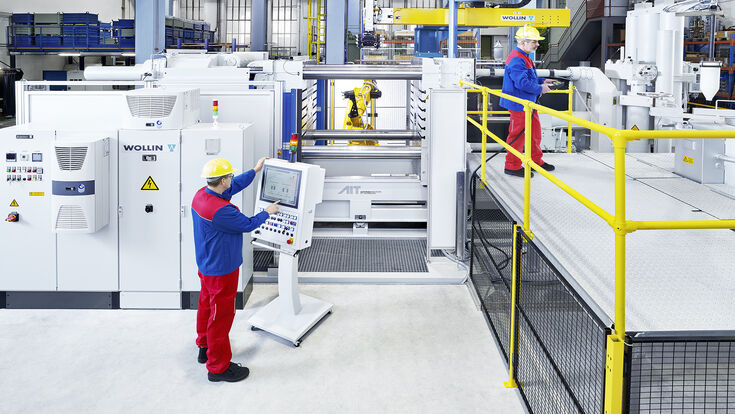
Lieferte die Prozesswerte für envIoTcast: Druckgussmaschine am AIT LKR Ranshofen
- © AIT/LKRDie Dekarbonisierung und Transformation des industriellen Energiesystems ist ein wesentlicher Beitrag für das Erreichen der nationalen und europäischen Klimaziele. In der Industrie wurde bisher auf den Einsatz von CO2-neutralen Technologien anstelle von günstigem Erdgas aus wirtschaftlichen Gründen verzichtet. Doch aufgrund der aktuellen Preisdynamik sind klimaneutrale Technologien wirtschaftlich konkurrenzfähig geworden.
Das AIT Austrian Institute of Technology untersucht im NEFI-Projekt „envIoTcast – Environmentally Friendly Casting“, einem Forschungsprojekt im Automobil-Cluster der oberösterreichischen Standortagentur Business Upper Austria, mehrere Anwendungsfälle von energieintensiven Hochtemperaturprozessen. Dabei werden technisch und wirtschaftlich realisierbare Lösungen für den kurzfristigen und vollständigen Umstieg auf eine nachhaltige Energieversorgung konzipiert. „Wir haben mit NEFI die Möglichkeit, neue Technologien und Lösungen großflächig zu testen", schildert Wolfgang Hribernik, Head of Center for Energy am AIT und NEFI-Verbundkoordinator.
Grüne Gießerei 4.0
Im Projekt envIoTcast wird das moderne, nachhaltige Konzept der Grünen Gießerei 4.0 entwickelt und demonstriert. Die Herstellung von Gussteilen findet in Gießereien in mehreren einzelnen, sequenziellen Schritten statt: Schmelzen, Gießen, Wärmebehandlung und mechanische Bearbeitung. Zurzeit sind die einzelnen Produktionsschritte in heutigen Gießereien allerdings energetisch und informationstechnisch weitgehend voneinander getrennt und es findet keine gesamtheitliche Energieoptimierung statt. Dadurch wird eine vollständige Dekarbonisierung wesentlich erschwert.
Evaluiert werden mehrere Industriebetriebe hinsichtlich eines realisierbaren Umstiegs auf Erdgas-Alternativen. "Mit unseren Labors und Simulationsmethoden sehen wir, welcher Energieträger für den jeweiligen Industrieofen und Produktionsprozess eine klimaneutrale Alternative darstellt", sagt Christoph Zauner, Senior Scientist am AIT und Projektleiter. Herausgefunden wurde unter anderem, dass viele Öfen mit Ökostrom anstatt mit Erdgas beheizt werden können. Bei anderen kann auf grünen Wasserstoff, Biomethan oder synthetisches Methan umgestellt werden. Insbesondere bei hohen Temperaturen über 900 °C ist grünes Methan, das durch Methanisierung oder in Biogasanlagen hergestellt wurde, eine sehr gute Alternative.
"Großes Potenzial bergen zudem die Nutzung von Ofenabwärme und die Digitalisierung der Prozesse, wo bis zu 30 Prozent der Energie gespart werden können", heißt es im Projekt. Die großen Meilensteine des Projekts sind die Erhöhung der Energieeffizienz durch Reduzierung der Wärmeverluste und die verstärkte Abwärmenutzung, zentrale Steuerung der Prozesse sowie die vollständige Dekarbonisierung des verbleibenden Energieverbrauchs durch Umstieg auf CO2-neutrale Primärenergieträger.
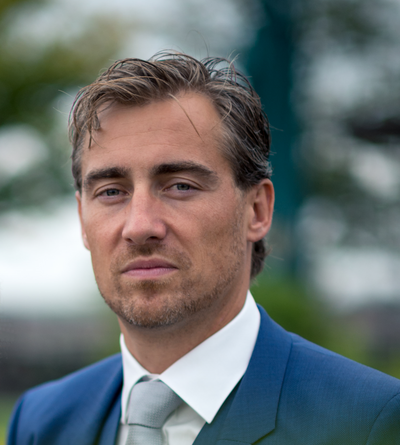
Gut zu wissen!
NEFI – New Energy for Industry ist Teil der „Vorzeigeregion Energie“ und verfolgt den Ansatz der Dekarbonisierung des industriellen Energiesystems mithilfe von Schlüsseltechnologien „Made in Austria“. Der NEFI Innovationsverbund hat sich um ein Konsortium aus AIT Austrian Institute of Technology, Montanuniversität Leoben, OÖ Energiesparverband und der oberösterreichischen Standortagentur Business Upper Austria formiert und bündelt die vielfältige Erfahrung im Bereich der Energieforschung und Umsetzung von Projekten.
Maßgebliche Unterstützung kommt von den beiden industriestarken Bundesländern Oberösterreich und Steiermark. Das ständig wachsende Konsortium mit aktuell mehr als 100 Partnern aus Unternehmen, Forschungseinrichtungen und öffentlichen Institutionen entwickelt in den ersten 17 Projekten technologische und systemische Lösungen, die die Energiewende in der Industrie ermöglichen sollen. Der Klima- und Energiefonds unterstützt die NEFI-Projekte mit 21,5 Millionen Euro, dotiert aus Mitteln des Bundesministeriums für Klimaschutz Umwelt, Energie, Mobilität, Innovation und Technologie (BMK).
www.nefi.at
Use Case voestalpine.
Zusammengefasst: Die ersten Ergebnisse würden zeigen, dass auch bei energieintensiven Bereichen wie in der Stahl- und Aluminiumverarbeitung fossile Energieträger "vollständig durch Erneuerbare ersetzt werden können", sagt AIT-Experte Wolfgang Hribernik.
Einer der realen Anwendungsfälle in der Grünen Gießerei 4.0 ist die Dekarbonisierung von Industrieöfen, wie sie in der Stahlweiterverarbeitung der voestalpine Anwendung findet. Konkret werden diese Dekarbonisierungspotenziale bei den Wärmebehandlungsaggregaten der Anlagen bei unterschiedlichen voestalpine-Standorten untersucht. Hier können aus den Erkenntnissen von envIoTcast einige Ansatzpunkte wie das Vorwärmen von Produkten oder die Etablierung eines thermodynamischen Modells für die Prüfung von verschiedenen Verbesserungsansätzen übernommen werden. Für die Wärmebehandlung von Metall im Zuge der Stahlweiterverarbeitung gibt es nicht die EINE Alternative zu Erdgas. Vielmehr stellt sich die Frage, welcher Energieträger für den konkreten Einsatz, der am besten geeignete ist. Ökostrom, Biomethan, das durch Reinigung von Biogas erzeugt wird oder Methan, das durch Synthetisierung mit Wasserstoff und CO2 hergestellt wird, werden zukünftig zentrale Heizmedien für Industrieöfen sein.
CO2 im Kreislauf.
Wird Erdgas in Industrieöfen verbrannt, entsteht ein Rauchgas, das etwa 15 Volumsprozent (vol%) CO2, 15 vol% H2O und 70 vol% N2 enthält. Der CO2-Anteil kann mit erprobten Technologien abgetrennt werden und mit grünem Wasserstoff wieder zu Methan (CH4) „methanisiert“ werden. Dieses „grüne Methan“ kann dann erneut ohne jegliche Prozessumstellung im Ofen verbrannt werden. So ist ein Kreislauf möglich, bei dem kein CO2 in die Atmosphäre gelangt. Derartige Anlagen sind mit heutigen Komponenten bis in den 100-MW-Bereich bereits realisierbar und im 10-MW-Bereich bereits seit Jahren erfolgreich in Betrieb.
17 Projekte
Die Vorzeigeregion NEFI zeigt mit ihren 17 Projekten, dass mit in Österreich entwickelten Energietechnologien eine 100-prozentige erneuerbare Energieversorgung der Industrie möglich ist. Neben dem verstärkten Einsatz erneuerbarer Energie und der Steigerung der Energieeffizienz gibt es eine große Breite an Forschungsansätzen, um intelligente Energiekonzepte zur drastischen Reduktion von CO2-Emissionen zu erproben. „Das Besondere an unserer Zusammenarbeit ist, dass die neuen Technologien in Echtzeit im Feld erprobt werden können – wir forschen und entwickeln sehr nahe an der unmittelbaren Umsetzung. Das reduziert das technische und wirtschaftliche Risiko der Betriebe beim Einsatz neuer Technologien“, erklärt Wolfgang Hribernik, Leiter der NEFI-Verbundkoordination.
Das NEFI-Projekt envIoTcast unter Leitung des AIT Austrian Institute of Technology vereint Partner aus der oberösterreichischen Industrie und der Forschung wie die LKR Leichtmetallkompetenzzentrum Ranshofen GmbH, HOFMANN Wärmetechnik GmbH, Ing. Martin Johann Fischer und dem Automobil-Cluster in der oberösterreichischen Standortagentur Business Upper Austria. Die Projektlaufzeit ist von 03/2021 bis 02/2024.
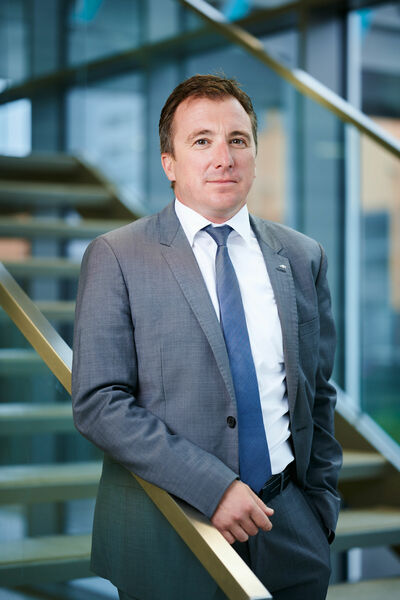
3 Learnings
Elektrifizierung
Insbesondere wenn die benötigten Ofentemperaturen unter 1.000 °C liegen und die Leistungsdichte relativ gering ist, können bestehende Gasbrenner durch elektrische Heizer ersetzt werden. Ebenso gibt es verschiedene Ofenkonzepte, die unterschiedlichen Produkte mittels Induktion erwärmen. Bei der nachträglichen Elektrifizierung muss auf ausreichende Temperaturhomogenität und Wärmeübertragung ins Produkt geachtet werden, was mittels 3D-Ofensimulationen berechnet werden kann.
Grüner Wasserstoff
In Öfen, bei denen eine höhere Leistungsdichte erforderlich ist oder elektrische Heizelemente im Nachhinein aus technischen Gründen nicht installiert werden können, muss weiterhin auf chemische Energieträger zurückgegriffen werden. Grüner Wasserstoff ist ein Beispiel dafür und kann grundsätzlich in Industrieöfen als Alternative zu Erdgas verbrannt werden. Er wird mittels Elektrolyse aus Wasser erzeugt. Entscheidend für einen wirtschaftlichen Betrieb ist einen möglichst günstigen, erneuerbaren Strom für die Elektrolyse zu verwenden. An manchen Standorten kann eine lokale Erzeugung auch in Österreich konkurrenzfähig sein, wenn entsprechende Flächen für Wind- oder Solarenergie zur Verfügung stehen oder Wasserkraft nahe ist. Direkte Stromleitungen von den Energieparks zur Industrie verringern die Kosten entscheidend, da die Netzgebühr gespart wird. Mittels Contracting und Power Purchase Agreements lassen sich sowohl auf Eigen- als auch Fremdflächen langfristig planbare, günstige Strompreise erzielen, wodurch Wasserstoffkosten im Bereich von ca. 3 €/kg (ca. 100 €/MWh) auch in Österreich möglich werden.
Grünes Methan
Der mögliche negative Einfluss der Wasserstoffverbrennung kann oft nur mit großem Aufwand geklärt werden. Doch selbst wenn die Produkteigenschaften unverändert bleiben, muss das in manchen Branchen erst im Zuge einer aufwändigen Re-Zertifizierung belegt werden. Daher wäre es sowohl aus prozesstechnischer als auch unternehmerischer Sicht wesentlich einfacher, weiterhin eine „Art grünes Erdgas“ als Brennstoff verbrennen zu können. „Erdgas besteht zu ca. 85-90 % aus Methan, weshalb die Aufgabe darin besteht, kostengünstiges grünes Methan zu produzieren. Dieses kann in den Öfen und Kraftwerken ohne jegliche Umstellung verbrannt werden“, sagt Projektleiter Christoph Zauner. Zur Herstellung von grünem Methan gibt es zwei Wege: 1. Biomethan aus biologischer Fermentation („Biogasanlagen“), insbesondere von Abfällen und 2. Methanisierung von CO2 und grünem Wasserstoff.