Kür der besten Produktion Österreichs : Fabrik2024: Härtetest bei zwei Vorfinalisten
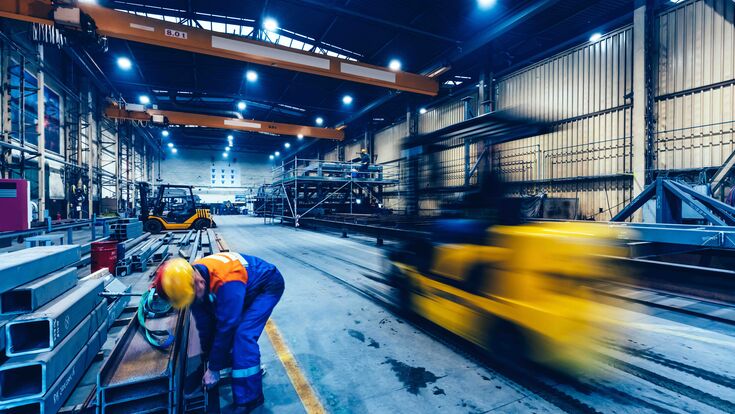
Zum 14. Mal schreiben Fraunhofer Austria und das INDUSTRIEMAGAZIN die renommierte Auszeichnung für Produktionsunternehmen in Österreich aus.
- © Adobe Stock"Große Dinge liegen hinter uns". Spult Helmut Schwarzl die vergangenen Monate gedanklich im Schnelldurchlauf ab, die radikale Optimierung des österreichischen Standorts Pottenbrunn, fällt sein Fazit eindeutig aus. "Da ist richtig die Post abgegangen". 150 Jahre ist der Konzern gerade alt geworden, hier in Pottenbrunn besteht das Sanitärtechnikunternehmen seit 1971. Lean Management wurde nach der Einführung 2007 so stark forciert, dass es heute selbstverständlich ist. Das ist das eine. Das andere ist ein recht epochaler Fünf-Jahres-Strategieprozess, der zuletzt umgesetzt worden ist.
"In Wahrheit haben wir die Produktion und das Prozesslayout komplett umgestellt", sagt Schwarzl. Der Fokus liegt nun auf einer Reihe von Hauptprodukten wie einem Rohrleitungssystem (Silent-PP) oder Dachentwässerungssystem (Pluvia), die im Wertstrom abgebildet sind - von der Urfertigung bis zum fertigen Produkt. 2023, also noch im Vorjahr, "hatten wir vergleichsweise instabile Prozesse und eine angespannte Auslastungssituation", sagt Schwarzl. Heuer geht sich allein in der Fertigung eine Produktivitätssteigerung von sechs Prozent aus - "da haben wir nachweislich gute Sprünge gemacht, für die wir durch Fraunhofer Austria externe Bestätigung suchen", so der Geberit-Chef des Werkes Pottenbrunn.
Führungsspannen kleiner
Die Motivlage für die Teilnahme ist damit geklärt, die Fülle der umgesetzten Maßnahmen gerademal skizziert. So wurden auch die Wege der anderen Produkte optimiert - "dort ziehen wir die Komponenten notwendigerweise über das Lager und nicht über den Supermarkt", sagt Schwarzl. Ferner wurde der Organisationstyp umgestellt. Die Führungsspannen sind nun kleiner. Meister wurden unter dem Motto "Führen vor Ort" an ihren Hauptarbeitsplatz - die Fertigung - gebracht, sie sitzen "nicht mehr irgendwo im Büro", so der Manager. Dank der Fertigungssteuerung über Kanban habe sich das Unternehmen deutlich verschlankt. Nicht nur Durchlaufzeiten wurden massiv reduziert, durch den Abbau von Puffern wurde Komplexität im Prozess abgebaut und Fläche gewonnen. "Die Hülle ist, wenn man so will, immer noch die gleiche, mengenmäßig haben wir uns verdoppelt", sagt Schwarzl. Mit Auswirkungen auch auf die Umschlaghäufigkeit im deutschen Zentrallager. Dort wird nun bei gleicher Lagerfläche einiges mehr an Volumen gemanagt. Belegt auch S/4HANA, auf das der Konzern setzt.
Aus- und Umbau
120 Maschinen, sagt Schwarzl, wurden im Zuge der Umstellung angefasst und neu positioniert. Die Spritzgießtechnik wurde auf drei Hallen ausgebaut. Dazu wurden auch "Spielchen mit 3D-Brillen" unternommen, die Möglichkeiten der Simulation genutzt. AI? Steht im Qualitätsmanagement des Unternehmens mit 410 Produktionsmitarbeitern, dessen aktuelle Quartalsperformance laut Führungsspitze gut sei, gerade am Beginn. Flexibilität wird dem Personal - man beschäftigt keine Leiharbeiter - abverlangt. Mitarbeiter wechseln zwischen den Linien und "federn damit tägliche Auftragsschwankungen ab", sagt Helmut Schwarzl. Roboter waren früher noch eine Randerscheinung am Standort. Heute sind 35 Stück im Einsatz, nicht zuletzt bei der Montage von Rohrleitungssystemen. Und fahrerlose Transportsysteme eilen durch die Hallengänge.
Weniger Verpackung
Auch beim Thema Nachhaltigkeit will Geberit punkten. Seit vielen Jahren verwenden die Niederösterreicher Abwärme für die Heizung, Gas ist eine verschwindend geringe Energieform. Die Hochpreisphase bei Strom "haben wir durch weitsichtigen Einkauf gut überstanden", sagt Schwarzl. Ein eigenes Energieteam sucht das Werk zudem laufend nach Potenzialen ab. Verpackungsverringerung ist ein Stichwort - QR-Codes ersetzen Etiketten und Montageanleitungen aus Papier. Am Ende gilt auch hier: Die Lean-Kultur ist kein Selbstläufer, muss jeden Tag neu erarbeitet werden. Gemba Walks und Trainings für Potenzialträger sind somit fest verankert in der Unternehmensstrategie.
Fabrik2024 - Der Preis für die effizienteste Produktion
Zum 14. Mal schreiben Fraunhofer Austria und das INDUSTRIEMAGAZIN die renommierte Auszeichnung für Produktionsunternehmen in Österreich aus.
Unter anderem diese drei Unternehmen - Geberit Österreich in Pottenbrunn, GW St. Pölten (ebenda) und Palfinger in Lengau stellen sich im Sommer der Vor-Ort-Evaluierung durch Experten von Fraunhofer Austria.
Bis Ende Juni bewarben sich Unternehmen durch Einreichung eines schriftlich ausgefüllten Fragebogens für die Wettbewerbsteilnahme.
Bis Mitte August laufen auf Basis dieser ersten Vorselektion in den Fabriken der Teilnehmer Vor-Ort-Evaluierungen durch ein Expertenteam von Fraunhofer Austria.
Am 3. Oktober stellen sich die Finalisten der hochkarätig besetzten Hearing-Jury. Dabei werden der Gesamtsieger der „Fabrik2024“ sowie die Gewinner der drei Wettbewerbskategorien „Efficient Factory“, „Smart Factory“ und „Green Factory“ prämiert. Das Finale samt anschließender Siegerkür findet bei Engel Austria in St. Valentin statt, zuvor wird es eine Werksführung beim Vorjahressieger geben.
Mehr Informationen hier
Gut geölte Regelkreise
Auch beim Auftragsfertiger GW St. Pölten Integrative Betriebe – ein Industriebetrieb mit rund 580 Mitarbeitern, drei Viertel davon Menschen mit Behinderung – ist die Lean-Kultur "organisatorisch sehr gut verankert", schildert Christian Mosböck. Er ist KVP- und Lean-Experte für die Produktionsbereiche im Unternehmen, das in den Geschäftsfelder Elektro, Metall, Schilder, Druck, Werbetechnik, GW Services und Textil tätig ist. "Die Regelkreise funktionieren", sagt Mosböck. In Sachen Reifegrad sieht er das Unternehmen auf der fünfstufigen Skala bei einer guten Vier.
Die Krux im Umgang mit dem zentralen Element KVP sei aber natürlich, sich "niemals zufrieden zu geben bei Qualität, Nachhaltigkeit, Kompetenzaufbau", sagt Mosböck. Seit 2011 ist er im Unternehmen, er kennt die Historie gut: Durch die Wirtschaftskrise 2008 verlor die GW St. Pölten einige große Kunden und dies brachte einen Umsatzrückgang mit sich. Der daraus resultierende Leidensdruck erwirkte einen Change-Prozess im Unternehmen in Bezug auf Lean- und Prozessmanagement. KVP-Vorschläge werden heute – quer durch alle Fachbereiche – digital eingebracht. "Eine absolute Erfolgsgeschichte", sagt Mosböck. Was die Niederösterreicher auch gut beherrschen: Das Prozessmanagement und die Integration in die Wertschöpfungskette der Kunden, wie etwa Kanban-Vereinbarungen oder Auftragsrealisierung direkt am Kundenstandort. Anderswo – etwa wenn es um die Polsterung von hochwertigen Stühlen geht – läuft die Auftragsabwicklung individueller. " Von der Bestellung per EDI-Anbindung bis zumPapierformular reicht die Bandbreite.
Wo stehen wir
Die Teilnahme am Fabrik-Preis soll eine Standortbestimmung und ein Benchmark mit anderen Unternehmen bringen. "Wo stehen wir und welche Potentiale haben wir noch nicht ausgeschöpft", fasst es Mosböck in Worte. Wandlungsfähigkeit haben die im Metallbereich sehr stabil aufgestellten Niederösterreicher, die 5S leben, freilich schon mehrmals bewiesen. So wurde in Covid-Zeiten rasch eine wertstrombasierte Schutzmaskenproduktion im Geschäftsfeld Textil auf die Beine gestellt, um zum einen Arbeitsplätze zu sichern und zum anderen die Umsatzrückgänge zu kompensieren. Und nach einem starken Umsatzrückgang bei einem großen Kunden im Vorjahr – man lieferte Vorhänge – wurde kurzerhand ein neues Leistungsspektrum etabliert: "Wir fertigen jetzt hochwertige Polsterungen für Raumausstatter und Möbelhersteller", sagt Mosböck.
Digitalisieren - und Jobs erhalten
Ein Schwerpunkt ist die Nutzung von digitalen Technologien. Diese werden vor Einführung darauf überprüft, welchen Einfluss die Umsetzung von Digitalisierungslösungen auf die Beschäftigung behinderter Mitarbeiter hat und welche Chancen sich dadurch ergeben. "Mitarbeiter unterstützen und nicht ersetzen", ist das Motto. Vollautomatisierung ist demnach kein anzustrebender Zielkorridor. Die Einführung Fahrerloser Transportsysteme "würden wir uns mehr als einmal überlegen, weil wir den Job des Staplerfahrers erhalten wollen", sagt Mosböck. Digitale Infoboards in der Produktion, um auch Verbesserungsvorschläge einzumelden, seien dagegen im Sinne der GW St. Pölten.
"Wir streben hier eine papierlose Produktion an", sagt der Lean-Experte. Ein Corporate Wiki enthält das Management-Handbuch und Prozessanweisungen, ist rasch und unbürokratisch zu aktualisieren und hält die Belegschaft mit Informationen und Neuigkeiten mittels Blogs am laufenden. Ein Wort noch zur betrieblichen Nachhaltigkeit. Eine PV-Anlage ist am Standort Gmünd in Betrieb genommen worden, am Standort St. Pölten in Planung. Die neu installierte Kompressoranlage wird zusätzlich gerade um eine Wärmerückgewinnung erweitert. Ebenfalls aktuell: Zahlreiche Optimierungsprojekte im Zusammenhang mit Energieeffizienz, Nachhaltigkeit und Ressorucenschonung.
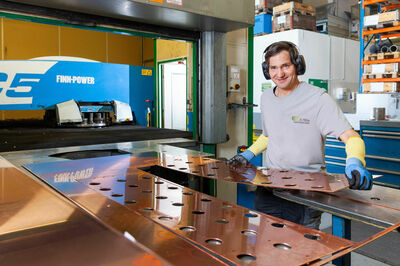