Messen statt Schätzen : Energieeffizienz durch synthetische Schmierstoffe
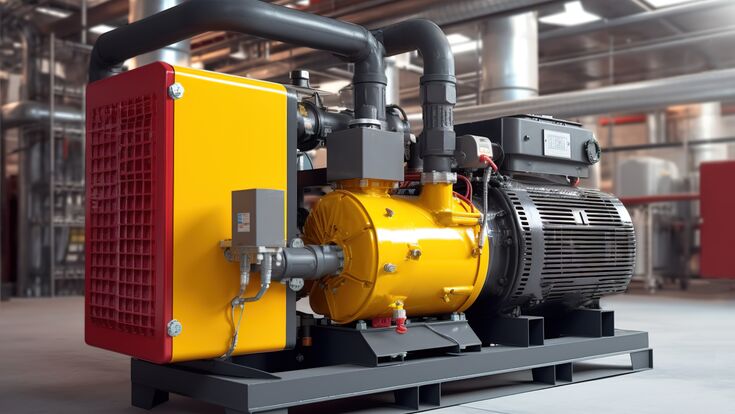
Die Umstellung auf synthetische Spezialschmierstoffe spart Energie, reduziert die Serviceintervalle und verlängert die Lebensdauer von Maschinen.
- © stock.adobe.comDer Ölwechsel dauerte ein paar Stunden, obwohl der Kompressor, der von einem großen österreichischen Betrieb aus der Lebensmittelindustrie genutzt wird, nicht gerade klein ist. Es wäre noch schneller gegangen, hätte das Technikerteam vor dem Einfüllen des neuen synthetischen Schmierstoffs nicht erst einmal die alten Verschmutzungen, die sich im Laufe der Zeit im Kompressor gebildet haben, entfernen müssen.
Das sei kein untypisches Szenario, erklärt Markus Mair, Anwendungstechniker beim Schmierstoffspezialisten Klüber Lubrication. „Bei Mineralölen bilden sich schneller Ablagerungen als bei synthetischen Alternativen, dementsprechend höher ist die Verunreinigung im System. Der Umstieg auf synthetische Schmierstoffe entschärft auch dieses Problem.“
Weniger Verlustenergie
Durch die Verwendung von synthetischen Schmierstoffen lässt sich zudem die Temperatur in der Anwendung in vielen Fällen senken. Niedrigere Betriebstemperatur bedeutet: weniger Verlustenergie und damit größere Maschineneffizienz, niedrigere Stromkosten und auch eine bessere Klimabilanz. So weit, sagt Mair, sind die Zusammenhänge jedem, der in Technik und Maschinenbau zuhause ist, klar.
Doch die Effekte genau zu beziffern, sei eine überaus spannende und gar nicht so einfache Angelegenheit. „Oft wird bloß der Temperaturunterschied gemessen und daraus eine theoretische Energieeinsparung abgeleitet. Das ist zwar nicht völlig falsch, am Ende vergleicht man aber doch Äpfel mit Birnen. Denn die tatsächliche Einsparung kann nur direkt an der Maschine unter den individuellen Prozessbedingungen ermittelt werden.“
Genau das macht Klüber Lubrication. Genützt wird dazu eine eigene Lösung, die neben der Optimierung der Schmierstoffauswahl selbst und der Identifizierung aller Einsparpotentiale eine professionelle Messung der Energieaufnahme im Ursprungszustand und eine Messung nach der Umstellung beinhaltet. Wichtig dabei: Die Messung entspricht international anerkannten Standards, wie der DIN ISO 50015 und ist konform mit dem für Auswertungen dieser Art als Goldstandard geltenden International Performance Measurement and Verification Protocol (IPMVP). Auf diese Weise können, die durch den Schmierstoffwechsel eingesparten Kilowatt exakt und nachvollziehbar ausgewiesen werden.
Längere Serviceintervalle
Bei dem österreichischen Lebensmittelproduzenten, bei dem Klüber die Umstellung unterstützte, waren es am Ende vier Prozent, um die man den Energieverbrauch reduzieren konnte. Wichtig war in dem konkreten Fall aber auch die deutliche Verlängerung der Service- bzw. Ölwechselintervalle. 70 Liter Schmierstoff braucht der betroffene Kompressor, um funktionieren zu können. Solange Mineralöl verwendet wurde, war alle 8.000 Betriebsstunden ein Ölwechsel fällig.
Durch den Umstieg auf eine synthetische Variante, Klüber Summit SH 46, gelang es, die Wechselintervalle um mehr als das Fünffache zu verlängern, was zu weniger Betriebsunterbrechungen, deutlich geringeren Entsorgungskosten und auch zu einem reduzierten Personalaufwand führte. In Summe amortisierte sich das Projekt bereits innerhalb von drei Monaten und bringt dem Unternehmen inzwischen beträchtliche jährliche Einsparungen.
Kleine Beträge summieren sich
Auch die Umstellung von kleinen Maschinen lohnt sich, wie Markus Mair betont. Er nennt als Beispiel ein relativ kleines Getriebe mit einer Füllmenge von wenigen Litern und einer maximalen Energieaufnahme von 40 Kilowatt. „Das mag auf den ersten Blick nach keiner besonders großen Zahl klingen, doch zum einen geht es gerade heute im globalen Wettbewerb um jeden Cent und jedes Gramm CO2. Und zum anderen haben viele produzierende Unternehmen deutlich mehr als nur ein baugleiches Getriebe im Einsatz und dann können die Einsparungsbeträge schnell multipliziert werden.“
Verbesserte Klimabilanz
Weniger Energieverbrauch bedeutet klarerweise auch eine bessere Klimabilanz. Im eingangs erwähnten Beispiel in der Lebensmittelindustrie 12,5 Tonnen CO2-Einsparung pro Jahr und Kompressor. Dank der geringen Investitionskosten kann gerade bei kleineren Kompressoren außerdem eine kurze Payback-Zeit von gerade einmal zwei Monaten erreicht werden.
Freilich: Aus vergangenen Projekten genaue Aussagen zu Amortisationszeiten und exakten Energieeinsparungen abzuleiten, ist schwierig. Aus diesem Grund empfiehlt Markus Mair vor dem Start von Energieprojekten stets eine ausführliche Bestandsaufnahme und Beratung durch Experten. „Bei Projekten, die Klüber Lubrication mit seinen Kunden durchführt, ist das Standard. Nach einer solchen Bestandsaufnahme können wir in den allermeisten Fällen bereits genauere Abschätzungen darüber treffen, mit welchen Kosten und welchen Vorteilen der Kunde bei einer Umstellung auf unsere Spezialschmierstoffe rechnen kann.“